LIUNA Training and Education Fund
Overview
LIUNA Training and Education Fund (LIUNA Training), an NCCRS member since April 2016, is the training arm of the Laborers’ International Union of North America (LIUNA). LIUNA Training was formed as a labor-management trust fund in 1969, and its mission is to provide products and services that improve the lives of over a half million LIUNA apprentices and journeyworkers, and to improve the competitive position of LIUNA and its signatory contractors. LIUNA Training supports a network of more than 70 affiliated local and regional training funds in the U.S. and Canada. From developing and distributing curriculum, to training its trainers, to procuring and disbursing federal grant funding, LIUNA Training offers an array of quality services. LIUNA Training is accredited by the International Accreditation Service (IAS) for its processes for developing curriculum and training trainers.
The key to successful trade training and education are accomplished instructors. LIUNA Training provides career-long professional development and certification programs based on best practices in adult education. LIUNA Training is accredited by the American National Standards Institute (ANSI) as a certifying body of personnel for both LIUNA instructors and apprenticeship coordinators. The scope of this accreditation ensures the highest level of learning experience for apprentices and journeyworkers. LIUNA Training’s materials are available only to its network of affiliated funds. For information about student records, please email liunatraining@liunatraining.org.
Students and admissions representatives please note: NCCRS does not provide transcripts. Transcript requests and inquiries should be directed to the organization offering the courses, examinations or apprenticeship. See the Source of Official Student Records in the sidebar near the top right side of this page.
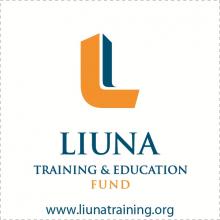
Titles of all evaluated learning experiences
Descriptions and credit recommendations for all evaluated learning experiences
Commercial Building
32 hours.
April 2011 – Present.
Upon successful completion of the course, students will be able to: list six different types of drilling applications and identify the appropriate type of drilling technique needed in each application; identify the most common types of aboveground drilling equipment and describe their uses; identify at least three aboveground drilling job site hazards and methods to control each hazard; list the health hazards of aboveground drilling and describe a method to control each hazard; identify and demonstrate the use of personal protective equipment (PPE) needed for aboveground drilling work; identify the class of several types of explosives; name the categories in the Bureau of Alcohol, Tobacco and Firearms (BATF) explosive classification system and give at least one example of a material in each category; identify the appropriate safety precautions for storing, transporting, handling, protecting and drilling around explosives; give examples of at least three tools that are powered by compressors; identify the components of airlines and fittings and demonstrate methods for connecting and securing them to tools and other fittings; list at least three precautions to take when working with a compressor in extreme temperatures; using a set of typical compressor problems, match troubleshooting checks with each problem; describe three types of drilling; identify the principal components of a drill string and describe the purpose of each; identify at least three drill bits and describe where they work best; list two causes of “bound steel” and at least one method to prevent each; describe and demonstrate the steps to “collar a hole”; list at least three factors that affect proper alignment of a borehole; describe and demonstrate the steps to add drill steel and remove drill steel from the drill string; describe at least two problems that prevent the flushing and removal of cuttings and at least one method to prevent each problem; describe at least two maintenance or critical operating practices that will prolong the life of the drill string; describe and identify the three most common types of rock; describe at least two types of borehole patterns and demonstrate how to lay them out; describe the safety hazards associated with operating a jackhammer and give at least one method to control each hazard; identify the components of the jackhammer’s lubrication system and demonstrate the proper lubricating procedures using the proper tools, materials and equipment; identify four types of bits used with jackhammers and give descriptions of each; demonstrate operation of a jackhammer; describe and demonstrate techniques for collaring and drilling a hole; explain the purpose of clearing cuttings from the borehole; and list five common problems that occur when drilling with a jackhammer.
Major topics include: the care and use of tools and equipment, as well as drilling techniques. Basic information about rocks and their composition and characteristics is introduced, as drillers must know how geology affects the drilling process. The personal safety of CCL's working on a drilling site is reviewed in depth. Site safety, health hazards, personal protective equipment, and working around explosives are also covered.
In the associate/certificate degree category, 2 semester hours in Construction Technology (4/16) (4/21 revalidation).
32 hours.
April 2011 – Present.
Upon successful completion of the course, students will be able to: describe what asphalt is and how it is made; list six modern-day uses for asphalt; identify and explain the proper care and use of nine asphalt hand tools; identify 10 types of heavy equipment used on asphalt jobs and explain their use; explain the responsibilities of the five work classifications of a typical asphalt crew: shovelers, rakers, screed man, paver operator and roller operator; demonstrate the proper method for shoveling and raking asphalt; explain and demonstrate the proper method for repairing a pothole; explain the reason for sealing asphalt surfaces and cracks; list and identify at least four hazards on an asphalt worksite and describe at least one method for eliminating or avoiding each hazard; list and identify nine types of protective clothing and equipment used when working with asphalt and explain the purpose of each; list and describe two asphalt pavement methods; calculate equipment and material needed for an asphalt-paving job using various jobsite scenarios; describe the operation and purpose of a floating screed; list and describe the tasks performed on a paving project; list and describe the three phases of asphalt compaction; list and identify the three categories of asphalt damage and explain the method of repair for each; describe and demonstrate the four steps for sawing a full depth asphalt patch; explain the role of pavement milling in performing partial depth asphalt repair; describe and demonstrate the seven steps required when performing skim patch repairs; describe the procedure for constructing a bridge approach; and demonstrate the set-up and calibration of electronic grade and slope control.
Major topics include: safety precautions necessary when working with, raking and placing asphalt, preparation of the surface, job preparation, and cleaning of the tools and machinery and patching of potholes and cracks, along with proper raking techniques.
In the lower division baccalaureate/associate degree category, 2 semester hours in Construction Methods and Materials, and Construction Math (4/16) (4/21 revalidation).
40 hours.
April 2011 – Present.
Upon successful completion of the course, students will be able to: describe the difference between a transit and a level; identify three types of advanced layout instruments used; list and demonstrate proper hand signals; identify the components of a field book, and describe the purpose of each; record information in a field book neatly and accurately; identify six tools commonly used in surveying procedures; measure the distance between two points using a surveyor’s tape or chain accurately to within ± /02'; measure from a given point and set a hub on a line; read and set angles on the vernier; given a point, correctly set up and level an instrument over the point; turn angles off of a base line and set new hubs; set up the instrument between two points; define the terms: angle, arc, baseline, chord, contour, diameter, radius, and right triangle; complete basic geometry problems on a worksheet and calculate area and volume for basic geometric shapes; accurately add and subtract angles; find the length of a vareity of objects using both the U.S. standard and decimal systems (80% correct) given common construction measuring equipment; convert measurements given in the standard system to their decimal equivalents; given a hand-held sight level (Locke level) device and a benchmark, find the elevation of various points; demonstrate basic surveying procedures for horizontal and vertical measuring, and controlling elevation with a margin of error not greater than .05" (five hundredths); given scenarios involving station designations on a construction site, calculate distances using station equations; given locations marked on a grid system, calculate their coordinates; explain the difference between in line and right angle referencing; describe the procedure for finding points from offset stakes; describe the procedure for finding both curb grade and top of curb elevation from the offset stakes; given dimensions from two known points, find a hidden point using swing tie referencing; find vertical and horizontal distances to a point from the information given on slope stakes; given a slope stake and the proper tools, set jump stakes showing the correct cut or fill along the slope; explain three types of slopes used on a roadway job and where and why each would be used; explain the procedure for making cuts and fills in a roadway construction project; explain the purpose of grade sheets and how they are used to find elevations for roadway construction; given a problem with earthmoving on a roadway project, find the number of cubic yards of dirt that will need to be cut or filled; given a problem with sub-base fill, find the tonnage of aggregate that will be needed; and given problems with quantities of surfacing material, find the tonnage of asphalt and the cubic yards of concrete that will be needed.
Major topics include the skills, knowledge and aptitude necessary to operate a variety of surveying instruments and to record information for maintaining elevation and alignment control points on heavy and civil construction projects.
In the lower division baccalaureate/associate degree category, 2 semester hours in Introduction to Surveying (4/16) (4/21 revalidation). NOTE: Course content is duplicative of the Construction: Total System Fundamentals course. Care should be taken to avoid awarding duplicate credit.
16 hours.
April 2011 – Present.
Upon successful completion of the course, students will be able to: recognize whether a surface is acceptable for an overlay; describe the tools and equipment needed for overlays; perform the steps of the overlay process, while maintaining all safety regulations, including prepping surface, mixing product, applying overlay, sealing overlay and scoring overlay; and identify solutions to common mistakes made in the overlay process.
Major topics include: criteria for concrete overlay application, different types of overlays, tools for the job, and work techniques. In small groups, participants mix, apply, stamp, stencil, score, and seal concrete overlays. Special emphasis is placed on practicing safe and correct work practices and identifying and using proper Personal Protective Equipment (PPE).
In the associate/certificate degree category, 1 semester hour in Construction Technology (4/16) (4/21 revalidation)
24 hours.
April 2011 – Present.
Upon successful completion of the course, students will be able to polish a concrete surface to a specific degree of shine and smoothness when given the proper tools and equipment.
Major topics include: two methods of concrete polishing, types of pads, hardeners and densifiers, and the tools and equipment used to polish concrete. Participants are given ample opportunity to learn and practice polishing techniques using hand-held and walk-behind polishers. Special emphasis is placed on practicing safe and correct work practices, identifying health hazards and using personal protection equipment.
In the associate/certificate degree category, 1 semester hour in Construction Technology (4/16) (4/21 revalidation).
40 hours.
April 2011 – Present.
Upon successful completion of the course, students will be able to: list the three most common types of concrete work; define the following terms: grade, sub-grade, foundation/footing, slab, finished grade, batterboards and string lines; lay out a batter-board and string-line setup for a slab using a leveling instrument to establish proper grade; calculate volume quantities for regular and irregular shapes to within 0.02 cubic yards; calculate the amount of concrete needed for various concrete forms of certain dimensions; describe and identify basic hardware, tools and common forming systems; describe three safety hazards associated with concrete formwork operations and describe at least one action to take in preventing each hazard; given a drawing of a slab to be built, list the tools, equipment, hardware and materials needed to lay out and build the formwork for the slab; given the necessary tools, hardware and materials, lay out and build the formwork for a slab, wall and column to within 0.02” grade; describe at least two hazards of form removal and cleanup, and describe at least one method to protect against each hazard; demonstrate form cleaning, stacking and storage procedures; describe five basic types of Portland cement and the uses of each; list five common concrete admixtures; describe the effects of each admixture in placement, consolidation, and finishing concrete; describe the primary health effect caused by skin exposure to cement, and identify the personal protective equipment (PPE) used to prevent skin exposure; describe five methods of transporting concrete to the placement area, and at least one situation that warrants each method; identify at least three tools used in concrete placement; describe three problems that can result from over-vibration of placed concrete and three problems that can result from under-vibration of placed concrete; demonstrate concrete placement techniques for slabs and walls; identify common tools used for finishing concrete and describe the purpose of each tool; describe three methods for curing concrete; demonstrate proper concrete finishing technique and at least one method of curing concrete.
Major topics include: the safety issues associated with the mixing, forming, placement, and curing of concrete materials, as well as the associated skills needed to prepare a site for concrete placement, building forms, estimating concrete quantities, concrete placement, consolidation and finishing, concrete repair, sawing, coring and drilling. Ample time is given for hands-on practice for all skills.
In the associate/certificate degree category, 2 semester hours in Construction Technology (4/16) (4/21 revalidation).
16 hours.
April 2011 – Present.
Upon successful completion of the course, students will be able to: describe the basic process of exposing aggregate in concrete using the seeding, brushing, and washing method; given the proper tools, equipment, and PPE, demonstrate the seeding method for creating an exposed aggregate finish on a freshly placed slab of concrete; describe three finishing techniques used to enhance the appearance of colored concrete; describe the basic process of stenciling freshly placed concrete; given the proper tools, equipment, and PPE, demonstrate the process of concrete stenciling on a slab of freshly placed concrete; describe the process of stamping freshly placed concrete; given the proper tools, equipment, and PPE, demonstrate the process of stamping concrete on a slab of freshly placed concrete; describe four factors that may affect the appearance of a stained concrete finish; and describe three applications for spray-top finishes.
Major topics include: various concrete finishes (exposed aggregate, colored concrete, stenciling concrete, and stamping concrete). Participants learn factors that affect the quality/appearance of each, materials used, processes for applying each finish, and health and safety factors. Participants observe, practice, and demonstrate the process for creating each decorative finish. Safety and proper work techniques are emphasized.
In the associate/certificate degree category, 1 semester hour in Construction Technology (4/16) (4/21 revalidation).
32 hours.
April 2011 – Present.
Upon successful completion of the course, students will be able to: define demolition and list three reasons for demolition activities; define three primary types of building demolition: mechanical demolition, “gut-out” demolition, and explosive demolition; define the concept of “deconstruction,” how it differs from demolition and why it can be preferable to demolition; identify at least three types of structures that may be subject to demolition; list at least three reasons why preplanning a demolition project is important and demonstrate the ability to complete the main requirements of a demolition work plan; identify at least two plans (other than a demolition work plan) needed to support a demolition project and define who is responsible for their implementation; state the importance of noise control and list at least three techniques for minimizing noise during demolition activities; describe two types of environmental issues that are important for demolition planning; list at least six general safety issues that are relevant during demolition operations; list at least four examples of special personal protective equipment that may be required when performing demolition or deconstruction activities and explain why; list and describe at least six hazardous materials typically found on a demolition/deconstruction job site where they are found, and what to do if you find them; describe at least three weather related hazards that may impact safety on a demolition/deconstruction job site and explain how to protect yourself from these hazards; identify at least four physical hazards that may be encountered on a demolition or deconstruction job and what you must do to make them safe; name at least three examples of confined spaces found on a demolition/deconstruction job site; name at least three types of emergencies and explain what should be done in each type of emergency; describe where to find the company’s emergency response plan; identify the OSHA regulations that apply to demolition site operations; state the purpose of site control; given a layout and options, demonstrate the purpose and application of barricades, warning tape, traffic cones, etc., when used during demolition/deconstruction activities; name three ways to increase effective site security to prevent damage and loss; list and describe the five main types of site control measures for a demolition or deconstruction project; name seven hazards to demolition workers posed by working around utilities; identify hazards that are posed by non-utility piping, such as sewers and chemical process lines, in industrial plants and explain how the risk can be reduced; explain why all utilities must be considered “live” until they are clearly disconnected or isolated; list common lockout/tagout procedures when working around electrical equipment; given a utility, identify who commonly is called on to locate its components; list at least four steps to take in the event of an emergency connected to utilities; describe the factors that impact the type of equipment selected for use in mechanical demolitions; list at least five safety considerations when working around mechanical demolitions; name eight types of equipment used for demolition and describe the capability of each; name at least four key roles that laborers play during mechanical demolition activities; list the five general types of special working conditions; list at least two hazards that may be encountered when performing water demolition work over and/or around water and describe ways to minimize the risks; describe the three different methods of chimney demolition; identify and describe at least three structural post-disaster hazards; identify and describe at least three biological post-disaster hazards; define deconstruction and demolition and explain how they differ; name three different types of demolition and describe each; list at least 10 commonly recoverable building materials and components; name at least five recyclable materials that can be recovered from building deconstruction; name at least four types of salvageable equipment; describe the typical sequence of deconstruction; list at least three safety issues and three safety measures related to performing deconstruction work; demonstrate the ability to remove several salvageable materials without damage.
Major topics include: planning projects, mechanical demolition equipment, material handling, site control, and special conditions that sometimes exist during this work. Particular attention is paid to safety in all aspects of the work.
In the lower division baccalaureate /associate degree category, 2 semester hours in Construction Methods and Materials, Construction Safety or Construction Technology (4/16) (4/21 revalidation).
45 hours.
April 2011 – Present.
Upon successful completion of the course, students will be able to: define the terms: global positioning system (GPS), latitude and longitude (the basis of global coordinates), and GPS system segments; describe the principles of operation of a GPS; list and explain the applications of a GPS; explain such GPS measuring techniques as static, differential, and real time kinematics; given a GPS system, demonstrate the setup and configuration of the base station and rover, and demonstrate the various measuring techniques according to the guidelines of this course; list and explain the potential errors that can be encountered when using a GPS; and when given a sample structure, to lay out and demonstrate the use of the GPS system and COGO (coordinate geometry) software functions.
Major topics include: the introduction of how GPS works and how it is used in construction, as well as how to set up and operate GPS using several measuring techniques. Students observe, practice, and demonstrate the use of the GPS system and COGO software for a sample structure. Special emphasis is placed on following proper procedures and developing safe work habits.
In the lower division baccalaureate/associate degree category, 3 semester hours in Introduction to Global Positioning Systems (4/16) (4/21 revalidation).
24 hours.
April 2011 – Present.
Upon successful completion of the course, students will be able to: describe and demonstrate five safe work practices related to rigging and hoisting; describe some of the common errors that cause most crane and rigging accidents; describe and demonstrate six safe work practices for working with and around cranes and explain why each is important; identify at least six different types of cranes; using scenarios involving cranes working near high voltage lines, give the minimum clearance between the crane and the lines based on OSHA standards; define the regulations that must be followed, and work practices that must by used, when using cranes to hoist personnel; solve problems involving linear distance, area, and volume using standard formulas; determine the load weights and centers of gravity for sample common construction materials of regular shapes using standard formulas; describe the effect that the sling angle has on slings and hardware; solve problems involving the calculations for sling tension for even legs, using standard formulas; identify the parts of a hoisting hook and describe the purpose of each; describe what might happen if a hook is “point loaded”; describe and demonstrate the inspection for hoisting hooks; identify five signs of damage to inspect for; identify six additional types of rigging hardware, describe the function of each, and describe how to inspect each piece of hardware; explain how to properly and safely attach each piece of hardware to the load or rigging as necessary; describe eight types of sling configurations and identify the situation that each is used in; using sample objects to rig, identify and rig each object with the most appropriate configuration; list and identify five materials used to make slings and under what conditions, identified through inspection, they must be removed from service; list and describe the three basic components of wire rope and define the purpose of each; identify four permanent markings that synthetic slings must have on them and explain the meaning of each; describe three situations that warrant the use of a signal person; describe five responsibilities of a signal person; describe the two methods of communicating with an operator; describe two essential practices a signal person should do before signaling and the importance of each; with the command for hand signals available, correctly perform at least 15 crane hand signals; and demonstrate the ability to communicate with an operator by using clear and precise voice commands.
Major topics include: the regulations included in federal, state, and equipment manufacturers’ standards. The course provides knowledge of these regulations, as well as an in-depth understanding of equipment, work procedures, techniques, and safety considerations that are essential for laborers to function in a zero-accident environment. Additionally, the course addresses training and certification requirements for riggers and signalers.
In the lower division baccalaureate /associate degree category, 2 semester hours in Construction Safety (4/16) (4/21 revalidation).
40 hours.
April 2011 – Present.
Upon successful completion of the course, students will be able to: demonstrate basic math skills; calculate area and volume; describe how to convert engineer rule measurements to standard rule measurements; demonstrate basic squaring principles; demonstrate basic survey skills using laser and field level; describe basic building code regulations for landscape irrigation systems; describe six different types of backflow prevention systems; demonstrate sprinkler layout; demonstrate and interpret actual sprinkler layout for installation purposes; demonstrate low voltage value and timer wiring; demonstrate flushing sprinkler systems before installing nozzles; demonstrate correct PVC glue/welding procedure; demonstrate troubleshooting wiring problems; and install low voltage lighting in designated areas.
Major topics include: basic math skills associated with landscape work, basic survey techniques, and a variety of water delivery systems. Several topics require students to perform tasks or demonstrate skills being taught. Special emphasis is placed on following proper procedures and developing safe work habits.
In the associate/certificate degree category, 3 semester hours in Basic Construction or Landscape Construction (4/16) (4/21 revalidation).
40 hours.
April 2011 – Present.
Upon successful completion of the course, students will be able to: implement a storm water pollution prevention plan; install various types of erosion control materials; interpret blue prints for grading and drainage; operate a laser level to correct elevations; operate a field level or transit; read grade stakes; set hubs and whiskers using grade stakes and lock-level with engineer’s rule; install drainage pipe and inlet box with correct percentage of fall; demonstrate cutting grade to within one tenth of a foot using grade stakes and a skip loader with a gannon scraper; and describe the importance of standard codes and local codes in reference to the direction of flow and earth moving permits.
Major topics include: the installation of proper drainage measures using a variety of tools and equipment, and the materials and skills associated with erosion control systems. Several topics require students to perform tasks or demonstrate skills being taught. Special emphasis is placed on following proper procedures and developing safe work habits.
In the associate/certificate degree category, 3 semester hours in Landscape Construction (4/16) (4/21 revalidation).
40 hours.
April 2011 – Present.
Upon successful completion of the course, students will be able to: identify four types of chain saws and their purpose; describe five hazards of chain saw operation and how they can be prevented; identify the kickback zone of the chain saw and list four ways to prevent or reduce this from occurring; demonstrate safe start up, inspection and operation of a chain saw; identify tools needed to sharpen a chain saw; demonstrate how to sharpen a chain saw; demonstrate the proper use of a circular saw; demonstrate knowledge and safe use of a chain saw, shredder, hedger and circular saw; identify various types of header and divider materials; install free-standing stone retainer wall; identify types of weed barriers for planter areas; and install and compact patio pavers.
Major topics include: skills necessary to use a variety of power tools commonly associated with landscape work. Students also learn to install hardscape items such as retaining walls and brick pavers. Several topics require students to perform tasks or demonstrate skills being taught. Special emphasis is placed on following proper procedures and developing safe work habits.
In the associate/certificate degree category, 3 semester hours in Landscape Construction (4/16) (4/21 revalidation).
Course 1: 40 hours. Course 2: 32 hours.
Courses 1 and 2: April 2011 – Present.
Course 1 and 2: Upon successful completion of the courses, students will be able to: describe the four safe work procedures that should be followed to ensure that masonry structures have adequate strength and/or stability; describe the three types of silicosis that can affect mason tenders; describe the four types of cement contact dermatitis that can affect mason tenders; describe the correct procedure for mixing water with acid; describe the types of Personal Protective Equipment (PPE) used by mason tenders and the hazards each type of PPE protects against; describe appropriate first aid procedures when given a description of an injury on a masonry construction project; describe the purpose of reinforced masonry construction; describe the functions of reinforcing steel and grout; describe the four types of reinforced masonry walls; describe how each type of wall tie and anchor is used in a masonry wall system; explain the purpose of flashing; given pictures or graphics of masonry construction or situations involving the installation of flashing, identify the areas where it is typically used; describe the purpose of control joints; given pictures or graphics of masonry construction or situations involving the installation of control joints, identify the areas where they are typically placed; explain the importance of accurately estimating masonry materials on a job; identify various types of brick and block; describe nominal dimensions in regard to estimation amounts of block and/or brick; calculate estimates for block and brick using the square foot method; calculate estimates for block and brick using the conversion method; estimate the amount of block and/or brick needed for a given project; given information on the layout (dimensions) and type of material used to construct multiple and various masonry projects, estimate the amount of block and/or brick needed for each project; explain the properties of masonry mortar; describe the characteristics of Portland cement mortars and masonry cement mortars; describe the seven types of mortar admixtures and their purposes; describe the four types of mortar mixing systems; given the appropriate materials and equipment, properly set up a power mortar mixer and mixing area; given the appropriate materials and equipment, accurately and correctly mix a batch of mortar, both manually and with a power mixer; given the appropriate materials and equipment, accurately and correctly mix a batch of colored mortar (both manually and with a power mixer); given the appropriate materials and equipment, accurately and correctly mix, place, and consolidate a batch of fine grout and coarse grout; given the appropriate materials and equipment, safely clean a power mortar mixer and mixing area; identify five hand tools that are commonly used when stocking block and/or brick; stock the materials necessary for the masons to begin construction on a masonry wall at ground level; demonstrate the ability to stock masonry materials on a scaffold for a masonry wall under construction; estimate the approximate amount of brick and block needed to complete a given section of wall; estimate he approximate amount of brick and block needed to complete a given section of wall; identify the proper personal protective equipment (PPE), tools, and equipment necessary for a mason tender; calculate the “cuts” necessary to maintain the bond in a masonry wall when given a set of masonry wall designs; describe the tasks required of a mason tender when performing housekeeping duties, equipment maintenance and shutdown; demonstrate the ability to “work the line” when given the setup, masons, and materials needed to construct a masonry wall by supplying and maintaining a consistent and quality mortar to the masons and correctly stocking materials and supplies as they are used; list the reasons mortar loses strength in cold weather; describe the types of materials that must be used during most cold-weather masonry construction; describe how masonry materials should be stored, heated, and placed during cold weather construction; explain the problems that may be encountered when constructing masonry in hot weather; list eight ways to reduce the effects of hot weather on masonry construction; explain five precautionary measures that can be taken to keep masonry walls clean; list three categories of cleaning failures; describe the different types of cleaning problems (i.e., efflorescence, white scum, green stain and brown stain); explain how cleaning failures can be prevented and cleaned; describe the proper method for cleaning a section of masonry wall using the following methods: bucket and brush hand cleaning, pressurized water cleaning and abrasive blasting; properly set up a stationary masonry saw; demonstrate the procedure for mounting and “ring testing” both a diamond blade and abrasive wheel; demonstrate how to maintain and clean a stationary masonry saw; perform the following types of cuts with a masonry saw: step cut, chop cut, cutting-head-positioned-down cut, and angle cut; demonstrate the proper donning and use of the personal protective equipment (PPE) needed when operating a masonry saw; describe at least 10 safe work practices that should be followed when operating a masonry saw; identify when masonry walls need to be braced; identify the components of a wall bracing system; calculate the maximum spacing between braces; identify the tools and materials needed for bracing a masonry wall; install all necessary bracing on a masonry wall under construction correctly and efficiently according to course guidelines; describe the three basic types of plaster; describe the various types of bases to which plasters can be applied; describe scratch coat, brown coat, and finish coat; describe the purpose and desired properties of both water and sand/aggregates when mixing gypsum plasters and stucco; and correctly and accurately proportion and mix gypsum base coat plaster, veneer plasters, and stucco with a mechanical machine and by hand.
Course 1 and 2: Major topics include: different types of masonry construction, masonry unit identification, material estimation and stocking procedures, the mason tender’s general duties, and the typical work that laborers perform on masonry construction job sites. Proper mortar mixing techniques, the use of admixtures, and the effect of weather on mortar are also addressed. Additionally, these courses provide instruction on how to safely brace newly erected masonry walls, present safety and health issues of the mason tender including silicosis, and address the use of proper personal protective equipment.
Course 1 and 2: In the lower division baccalaureate/associate degree category, 5 semester hours in Introduction to Masonry Technology (4/16) (4/21 revalidation). NOTE: Both courses must be successfully completed to gain access to credit recommendation.
24 hours.
April 2011 – Present.
Upon successful completion of the course, students will be able to: describe the steps for roadway construction; given a diagram of the layers of a road foundation, identify each layer 100% of the time; compare and contrast the advantages and disadvantages of the three major roadway surfaces: gravel, asphalt, and concrete; explain three types of slopes used on a roadway job and where and why each would be used; explain the procedure for making cuts and fills in a roadway construction project; explain the purpose of grade sheets and how they are used to find elevations for roadway construction; explain material shrinkage and swell; list the two main types of soil and explain which type of compaction equipment is best for each; given a problem with earthmoving on a roadway project, find the number of cubic yards of dirt that will need to be cut or filled; given a problem with sub-base fill, find the tonnage of aggregate that will be needed; and given problems with quantities of surfacing material, find the tonnage of asphalt and the cubic yards of concrete that will be needed.
Major topics include: parts of a roadway, road foundation, the slopes used, and the purpose of grade sheets in roadway construction. Students are also introduced to the two main types of soil and the compaction equipment that is best for each. Special emphasis is placed on following proper procedures and developing safe work habits.
In the lower division baccalaureate/associate degree category, 1 semester hour in Construction Methods and Materials (4/16) (4/21 revalidation).
40 hours.
April 2011 – Present.
Upon successful completion of the course, students will be able to: state OSHA’s definition of a scaffold; describe the following scaffold systems and list at least one use for each type: frame, tube and clamp, system, adjustable masonry, suspension, shoring, rolling tower, and elevated work platform; after reviewing scenarios of scaffolding accidents, describe at least five conditions that can cause a scaffold to fail; given job scenarios involving the loading of scaffold: determine if the scaffold is a light, medium or heavy-duty scaffold and calculate the maximum intended load for each; calculate the weight of specific sized rebar placed on scaffold; calculate the maximum allowable deflection for 8', 10', and 16' scaffold planks; describe two conditions that may overload a scaffold; list five conditions or situations that may cause shock loading; list five conditions that could lead to scaffold plank failure; describe how screw jack height affects scaffold stability; describe the function of mudsills when building a scaffold on unstable ground; using a diagram of a 5' wide scaffold, show the required location of tie-in points on the diagram; explain how a cold weather enclosure can increase the lateral (sideways) forces on a scaffold; list and identify at least eight tools that may be required when building scaffolds; match scaffold building tools with a description of their use; list at least five advantages of polypropylene rope; list at least five disadvantages of manila rope; given a demonstration and practice time, properly tie the following knots: clove hitch, bowline, triple bowline, half hitch, timber hitch, and scaffold hitch; describe four practices that can help maintain a rope; list and identify at least six PPE items that may be required when building scaffolds; identify at least three uses of tube and clamp scaffolding; explain at least two advantages of tube and clamp scaffold; list and identify the four basic components of tube and clamp scaffold; explain how each of the following items is used on a tube and clamp scaffold: post, runner, bearer, right angle swivel clamps, base plate, and diagonal brace; list and identify at least six tools that may be required to build tube and clamp scaffolding; given a tape measure, pencil, and tubes and clamps, demonstrate the ability to use the 3-4-5 method of squaring by attaching a runner and a bearer to a post at a 90º angle; given the proper tools and equipment, demonstrate the installation of posts, runners, bearers, and clamps for the erection of tube and clamp scaffolding according to the guidelines in this module and the manufacturer’s instruction manual; demonstrate the dismantling of the tube and clamp scaffold according to the guidelines in this module and the manufacturer’s instruction manual; identify at least four uses of systems scaffolding; compare the advantages and disadvantages of systems scaffold to tube and clamp scaffold; list and identify the seven basic components of systems scaffolding; explain how each of the following items are used on a systems scaffold: post or standard, bearer or transom, runner or ledger, base plate with screw jack, base collar with rosette, diagonal brace, and truss or putlog; list and identify at least six tools that may be required to build systems scaffolding; given the proper tools and equipment, demonstrate installation of posts, runners, and bearers for the erection of a systems scaffold according to the guidelines in this module and the manufacturer’s instruction manual; demonstrate safe dismantling of systems scaffold according to the guidelines in this module and the manufacturer’s instruction manual; match photos or drawings of scaffold components with their proper names; explain at least two advantages of walk-through scaffold frames; list and identify the four types of coupler pins used to lock frames together; describe how couplers are used when building scaffold; describe the two primary functions of screw jacks; explain the reasons for using mudsills; describe the difference between scaffold planks and platform decks; given the proper tools and equipment, build a level frame scaffold in each of the following configurations: straight run, straight run two bucks high, inside corner, and outside corner; demonstrate “bumping” planks from one level to another; and demonstrate the proper use of personal protective equipment (PPE) needed for scaffold building.
Major topics include: needs and responsibilities of a CCL responsible for building scaffolding on the job site or required to perform tasks while using scaffolding. Designed to meet the training requirements of 29 CFR Part 1926.454, the course includes frame, tube and clamp and systems scaffolding. Special emphasis is placed on following proper procedures and developing safe work habits.
In the associate/certificate degree category, 2 semester hours in Construction Technology (4/16) (4/21 revalidation).
32 hours.
April 2011 – Present.
Upon successful completion of the course, students will be able to: list two advantages of non-powered adjustable masonry scaffolding; list three ways that non-powered adjustable masonry scaffolding can increase worksite production; explain how each of the following items is used on non-powered adjustable masonry scaffolding: base towers, extension towers, elevating carriage, winch assembly, work platform, and cross braces; list the OSHA requirements for tying the scaffold into a wall; given the proper tools and equipment, demonstrate how to erect non-powered adjustable masonry scaffolding according to the guidelines in this module; demonstrate how to properly and safely dismantle the non-powered adjustable masonry scaffolding according to the guidelines in this module; list at least five types of job sites that may use powered mast-climbing scaffold; list five companies that manufacture powered mast-climbing scaffold in North America; explain how each of the scaffold components is used on powered mast-climbing scaffolding; list at least two reasons for having a firm foundation for a powered mast-climbing scaffold unit; given the proper tools and equipment, demonstrate the steps for erecting powered scaffold according to the guidelines in this module and the manufacturer’s operating manual; and demonstrate how to safely dismantle powered mast-climbing scaffold according to the guidelines in this module and the manufacturer’s operating manual.
Major topics are designed to address the needs of CCLs who are responsible for building scaffolding on the jobsite or are required to perform job tasks while using scaffolding. Created to meet the training requirements of 29 CFR Part 1926.454, the comprehensive program includes non-powered adjustable scaffold and powered mast-climbing scaffolding.
In the associate/certificate degree category, 2 semester hours in Construction Technology (4/16) (4/21 revalidation).
16 hours.
April 2011 – Present.
Upon successful completion of the course, students will be able to: describe some of the common errors that cause most crane and rigging accidents; describe and demonstrate six safe work practices for working with and around cranes and explain why each is important; identify at least six different types of cranes; using scenarios involving cranes working near power lines, give the minimum clearance between the crane and the lines based on OSHA standards; describe and demonstrate five safe work practices related to rigging and hoisting; identify seven types of rigging hardware and describe the function of each piece of the hardware; describe eight types of sling configurations and identify the situation that each is used in; describe the effect that the sling angle has on slings and hardware; describe the three situations that warrant the use of a signal person; describe five responsibilities of a signal person; describe the two methods of communicating with an operator; describe two essential practices a signal person should do before signaling and the importance of each; with the commands for hand signals available, correctly perform at least 15 crane hand signals; demonstrate the ability to communicate with an operator by using clear and precise voice commands.
Major topics include: signal person’s duties and responsibilities and include instruction in the proper techniques for giving voice commands and hand signals. The course also covers rigging basics and crane safety to ensure that qualified workers understand hoisting and rigging procedures that may affect the signal person’s actions and responsibilities.
In the associate/certificate degree category, 1 semester hour in Construction Technology (4/16) (4/21 revalidation).
40 hours.
April 2011 – Present.
Upon successful completion of the course, students will be able to: identify and describe the features of a Total Station; set up a Total Station over a point and orientate to a reference line; orient a Total Station to a reference azimuth; measure and record horizontal and vertical angles; measure and record horizontal and vertical distances; given locations marked on a site plan, determine their coordinates using a Total Station; given drawings or coordinates, lay out a simple structure using a Total Station; and given a Total Station, demonstrate routine care and maintenance procedures.
Major topics include: fundamentals of the modern Total Station, which enhance students assets to any employer involved in construction layout work. Students learn proper measuring techniques, how to plot coordinates, and the basics of using and maintaining a Total Station.
In the lower division baccalaureate/associate degree category, 2 semester hours in Introduction to Surveying (4/16) (4/21 revalidation). NOTE: Course content is duplicative of the Basic Line and Grade LINEG.HGC course. Care should be taken to avoid awarding duplicate credit.
16 hours.
April 2011 – Present.
Upon successful completion of the course, students will be able to: describe the supervisor’s responsibilities to help employees improve work zone safety; determine vehicles’ blind areas by mapping them out on the ground; demonstrate necessary steps to develop and implement a structured Internal Traffic Control Plan (ITCP); describe the principles and application of traffic control devices in order to implement a road user-friendly temporary traffic control set-up; identify, name and describe the uses of six different channeling devices used on highway work zone construction projects; determine whether channeling devices illustrated on a plan are used correctly based upon the presented application of use; match the symbols found on a typical application diagram key to their correct terminology; identify, list and quantify symbols found on six typical application illustrations; develop the correct phrasing for a Portable Changeable Message Sign (PCMS) given specific highway work zone situations; list and describe the four parts of a typical traffic control zone; select the proper traffic control device to match the work zone environment; list and describe three key elements in protecting pedestrians moving through a traffic control zone.
Major topics include: helping supervisors create a safe roadway construction work zone for workers and travelers by applying guidelines and developing structured processes for implementing internal and external traffic control plans. The course provides students with an understanding of the types of traffic control devices and how they are used, set up and dismantled.
In the lower division baccalaureate/associate degree category, 1 semester hour in Construction Management (4/16) (4/21 revalidation).
40 hours.
April 2011 – Present.
Upon successful completion of the course, students will be able to: describe the various types and purposes of tunnels; identify the parts of a tunnel; list the three main phases of tunnel construction; describe the different methods of tunnel construction and the conditions where each method would be used; describe three types of cut and cover tunnel construction techniques; explain the use of road headers and shields in soft ground tunneling; describe three types of tunnel boring machines (TBMs) and what they are used for; explain the main methods and equipment used in both hard rock and soft ground tunneling; explain the use of the New Austrian Tunneling Method; describe the use of microtunneling/pipe jacking and box jacking techniques; explain why tunnels are being constructed today; explain the kinds of utility lines Laborers install in tunnels; explain what is hauled in and out on the rail lines in tunnels; describe two ways muck is removed from a tunnel; list and describe six methods of ground support; explain the differences between jack leg, sinker, stoper and jumbo drills; explain the safety precautions for scaling; explain the different uses for shotcrete and grout in tunnel construction; explain why tunnel construction might involve more equipment cleaning and maintenance than aboveground construction; list at least five types of personal protective equipment required on a tunnel construction job site; explain the requirements for emergency lighting; explain safety precautions for lifting and carrying construction materials; explain what silicosis is, and how to prevent it; describe how to prevent cement burns; explain the purpose of a brass board; describe the responsibilities of a “top lander”; list locations on the surface and underground where barriers would be required, and types of barrier materials; demonstrate cap lamp/flashlight signals; demonstrate understanding of basic hand and voice signals for hoisting; describe how other means of signaling may be used to communicate hazards underground; describe types of electronic communications used in tunnels; explain the OSHA definition of a “competent person” and that person’s responsibilities on a tunnel job site; explain what parts of a tunnel jobsite must be inspected for safety, and how often; state the acceptable limits for oxygen content in the air in a tunnel; list some of the hazardous gases that can seep into a tunnel; explain when the air in a tunnel must be tested for flammable gases; demonstrate how to inspect and use a self-rescuer; explain the OSHA definition of a “confined space” and the precautions for working in a confined space; explain how to respond to flooding in a tunnel; explain when an employer must provide a tunnel rescue team, and how that requirement can be met; list safety requirements for personnel hoists; describe safety procedures for riding in mancars or mantrips; state the heights or ladder lengths when fall protection is required; list safety precautions for working around jumbo drills; describe how to use portable safety ladders; explain how to avoid being struck by a loci; list safety procedures for working around hoisted loads; describe the hazards of a TBM segment erector; list the steps of a lock out/tag out procedure; explain why housekeeping is important on a tunnel job site; explain why wet skin is a greater electrocution risk than dry skin; list safety guidelines for using extension cords; explain requirements for routing electrical cables in tunnels; list types of high-pressure lines used in tunnels; explain why a worker whose skin has been punctured by high-pressure material needs medical attention; explain safety precautions for using pneumatic tools; define ANFO and list the different forms it can take; define detonation cord; describe the responsibilities of an authorized blaster; explain safety requirements for moving explosives with hoists or elevators and with locis; explain safety procedures for tamping explosives into blasting holes; explain the required warnings for blasting areas and blasts; explain safety procedures for misfired explosives in boreholes; describe how to safely move gas cylinders; list requirements for fire extinguishers in tunnels; and explain what types of vehicle fuel can be used in tunnels.
Major topics include: introductory information about tunnels, how they are built, and the safety considerations involved with working on a tunnel construction job, including personal safety, communicating for safety, underground safety, safety around equipment, and safety around energy sources.
In the lower division baccalaureate /associate degree category, 2 semester hours in Construction Technology or Construction Safety (4/16) (4/21 revalidation).
Construction Craft Laborer (CCL) Core
175 hours of classroom instruction and 4,000 hours of supervised practical experience over two years.
April 2011 – Present.
Upon successful completion of the CCL Core and 4,000 hours of supervised practical experience, students will be able to: prepare, lay out, clean up, and secure a job site; use and understand basic blueprint symbols and views; recognize, secure, and maintain jobsite safety; identify and work safely around environmental hazards; erect, dismantle, maintain, and work from scaffolds or lifts; operate and maintain hand and power tools; operate and maintain equipment as required by the job; identify, estimate, move, supply, stock, and store materials; and use appropriate hand signals. Along with completing core work experience, students will complete on-the-job learning in one of the following areas of concentration: masonry, deconstruction/demolition, building construction, heavy/highway and utility construction, pipeline, tunneling, environmental remediation, and landscaping.
Major topics include: blueprint reading, building construction, confined space awareness, craft orientation, fall protection, first aid/CPR, general construction technology, hazard communication, OSHA construction safety and health, scaffold user, and flagger.
In the lower division baccalaureate/associate degree category, 18 semester hours, distributed as follows: 2 semester hours in Blueprint Reading, 4 semester hours in Construction Technology, 1 semester hour in Industrial Safety, 4 semester hours in Introduction to Construction, 1 semester hour in Applied Mathematics, and 6 semester hours in Field Experience (4/16) (4/21 revalidation). NOTE: Apprentices must successfully complete the CCL core comprised of 175 classroom hours and 4,000 hours of supervised practical experience over two years to gain access to college credit recommendations.
Environmental - LIUNA Training and Education Fund
40 hours.
April 2011 – Present.
Upon successful completion of the course, students will be able to: define the following trade related terms and acronyms: ACM, EPA, asbestos fiber, friable and non-friable asbestos-containing material, micron, OSHA, PACM, PEL, SM, TSI; list the six types of asbestos as identified by OSHA; list the two most common types of asbestos used in construction; explain the difference between friable and non-friable asbestos-containing materials; correctly state and explain the function of the OSHA permissible exposure limit (PEL) for asbestos; describe each of the four classes of asbestos work activity specified by OSHA; define the following terms: carcinogen, ingestion, inhalation, latency period, routes of entry, synergism; identify the two major routes of entry for asbestos into the body; explain the relationship between smoking and exposure to asbestos; list three diseases linked to occupational asbestos exposure and describe the symptoms of each disease; name the body organs affected by asbestos exposure and explain how asbestos affects each; list three protective mechanisms the body uses to get rid of asbestos fibers, and explain how these mechanisms work; define the following acronyms: FEV1, FVC, NIOSH, PFT; list the three reasons for establishing a medical monitoring and surveillance program; list the five required elements of an initial/preplacement medical examination for asbestos abatement workers; list the five required elements of an annual medical examination for asbestos abatement workers; list two additional recommended medical tests for asbestos abatement workers; state the number of years an employer must keep the medical records for each employee; list 10 legal rights workers have under the Occupational Safety and Health Act; list the seven responsibilities workers have under the Occupational Safety and Health Act; list seven steps workers should follow if they are punished for exercising any OSHA legal right; explain the purpose of the following EPA standards: NESHAP, AHERA, ASHARA; describe the following three air-purifying respirators (APR) used by asbestos abatement workers, and state the assigned protection factor (APF) for each: half-face APR, full-face APR, and powered APR; list and explain at least six limitations of APRs; list and describe the three filter series and three filter efficiency levels for particulate filters; explain the terms breakthrough and warning properties, and list four steps that should be taken if breakthrough occurs; explain the term assigned protection factor (APF) for a respirator; explain the acronym MUC as it relates to a respirator, and calculate the correct MUC for half-face, full-face, and powered air purifying respirators; explain the difference between an air-purifying respirator and an atmosphere-supplying respirator; explain the difference between continuous flow and pressure-demand regulators; state the correct APF for a continuous flow Type C airline; state the correct APF for a positive-pressure, pressure demand airline; given the proper personal protective equipment, correctly dress out for entry into an asbestos work area (containment); demonstrate the correct way to don a negative pressure respirator and perform a positive and negative user seal check; demonstrate the correct way to doff personal protective equipment in a three-stage decontamination unit; list and explain the nine requirements of a respiratory protection program; explain the difference between a qualitative and a quantitative fit test and give an example of each; define the following terms and acronyms: accident, confined space, engineering controls, GFCI, hazardous atmospheres, LFL, UFL, oxygen deficiency, lock out and tag out, personal fall arrest system, heat stress, personal hygiene; describe the different levels of heat stress and the dangers they pose to workers; given a variety of job site scenarios, demonstrate safe work practices around the following hazards: electrical, ladders, scaffolds, housekeeping, falls, confined spaces, hazardous atmospheres; describe the fire hazards that exist in a controlled area and how to prepare for the occurrence of an accidental fire; define the following terms and acronyms: clean room, equipment room, HVAC, shower room, waste load-out area; list and explain four reasons for preplanning asbestos abatement operations; list the 12 steps in preparing the work area; define the purpose of decontamination on an asbestos abatement project; list the elements of the decontamination chamber and explain the function of each; explain the purpose and function of a negative pressure air unit; given scenarios of spaces, calculate the number of machines needed to meet air change requirements; given the proper materials and equipment, demonstrate how to prepare the work area, set up the required number of negative air machines and set up a three-chamber decontamination unit according to course guidelines; define the following terms and acronyms: amended water, encapsulation, enclosure, glove bag, HEPA vacuum, NESHAP; describe the difference between bridging and penetrating sealants; list three advantages and seven disadvantages of encapsulation; list three advantages and seven disadvantages of enclosure; list 10 tools commonly used with a glove bag; describe the two stages of asbestos cleanup; list the 19 steps of the final cleanup; define the following terms and acronyms: aggressive sampling, air sampling, breathing zone, bulk sampling, PCM, personal sampling, PLM, static sampling, TEM; explain how and why air sampling is done on an asbestos abatement project; list the two analytical methods used in final clearance of asbestos abatement projects; explain the difference between static sampling and aggressive sampling; describe bulk sampling, settled dust sampling, and wipe sampling methods; list and describe the limitations of three analytical methods used in asbestos abatement; explain the purpose for taking area samples from outside the work are (but inside the building) and from outside the building; define the following terms and acronyms: ACBM, AHERA, bonding, contract, insurance, and tort liability; describe a good faith survey; describe a pre-bid walk through; list three types of bonds that are commonly issued in construction; list the three types of insurance that owners, consultants and contractors should have; list four types of contracts under which asbestos abatement projects are performed; identify three personnel roles on a large asbestos abatement project; explain the purpose of project plans, specifications, and contracts; give at least four examples of how they impact project planning; define the following terms and explain their purpose on an asbestos abatement project: production schedule, equipment schedule, bar chart; describe the role the supervisor plays in effecting safety, quality, and production on an asbestos abatement project; describe the supervisor’s role in fostering a working relationship with the union; list four things that should be planned for when setting up the job site; identify the five key points of communication; identify the three rules of dealing with interpersonal conflict; and list the behavior patterns that can be considered to be forms of sexual harassment.
Major topics include: work area preparation, decontamination facility construction and use, abatement techniques, and cleanup procedures. The course builds upon information provided in the Asbestos Abatement Worker course and prepares CCLs to supervise asbestos abatement projects. Participants receive extensive instruction and hands-on training in many subjects. Special emphasis is placed on following proper procedures and developing safe work habits. The course meets all OSHA requirements for supervisor level training and is mandatory for all persons who will supervise workers involved in Class I, and Class II asbestos abatement work. The course exceeds EPA’s 32-hour minimum course requirements stipulated under 40 CFR Part 763.
In the lower division baccalaureate /associate degree category, 2 semester hours in Industrial Safety (4/16) (4/21 revalidation).
40 hours.
April 2011 – Present.
Upon successful completion of the course, students will be able to: define the following trade related terms and acronyms: ACM, EPA, asbestos fiber, friable asbestos-containing material, micron, non-friable asbestos-containing material, OSHA, PACM, PEL, SM, and TSI; list the six types of asbestos as defined by OSHA; list the two most common types of asbestos used in construction; explain the difference between friable and non-friable asbestos-containing materials; state the OSHA permissible exposure limit (PEL) for asbestos; describe a Class I asbestos work activity; describe a Class II asbestos work activity; describe a Class III asbestos work activity; describe a Class IV asbestos work activity; define the following terms: carcinogen, ingestion, inhalation, latency period, routes of entry, and synergism; identify the two major routes of entry for asbestos into the body; explain the relationship between smoking and exposure to asbestos; list three diseases linked to occupational asbestos exposure and describe the symptoms of each disease; name the body organs affected by asbestos exposures and explain how asbestos affects each one; list three protective mechanisms the body uses to get rid of asbestos fibers, and explain how these mechanisms work; define the following acronyms FEV1, FVC, NIOSH, and PFT; list the three reasons for establishing a medical monitoring and surveillance program; list the five required elements of an initial/preplacement examination for asbestos abatement workers, the five required elements of an annual examination, and two additional recommended tests; list the five required elements of an initial/preplacement examination for asbestos abatement workers, the five required elements of an annual examination, and two additional recommended tests; list 10 legal rights workers have under the Occupational Safety Act of 1970; list the seven responsibilities workers have under the Occupational Safety and Health Act of 1970; list seven steps workers should follow if they are punished for exercising any OSHA legal right; explain the purpose of the following: EPA standards, NESHAP, AHERA, and ASHARA; describe the following three air-purifying respirators and list the assigned protection factor (APF) for each: Half-Face Air Purifying Respirator (Half-Face APR), Full-Face, Air Purifying Respirator (FFAPR), and Powered Air Purifying Respirator (PAPR); list and explain at least six limitations of APRs; list and explain the three filter series and three filter efficiency levels for particulate filters; explain the terms breakthrough and warning properties, and list four steps that should be taken if breakthrough occurs; explain the term assigned protection factor (APF) for a respirator and, given the five different respirators, state the correct APF in four of the five examples; explain the differences between an air-purifying respirator and an atmosphere-supplying respirator; explain the abbreviation MUC as it relates to a respirator, and calculate the correct MUC for at least four out of five sample respirators; explain the differences between the three delivery systems for breathing air: continuous flow, demand, and pressure demand; explain how a supplied airline respirator (SAR) works; list three limitations of the SAR and the APFs for both the SAR and the SAR with escape; explain how an open-circuit pressure demand SCBA works, its limitations, and APF; given the proper equipment, demonstrate the proper procedures for refilling an SCBA cylinder; list and explain the nine requirements of a Respiratory Protection Program; explain the difference between a qualitative and a quantitative fit test and give two examples of each; demonstrate and explain the proper procedure for performing a positive and negative user seal check on an APR; using a variety of respirators, demonstrate how to put on, use, take off, and maintain each respirator according to the guidelines of this course; define the following acronyms and terms: accident, confined space, engineering controls, GFCI, hazardous atmospheres, LFL, UFL, oxygen deficiency, lock out and tag out, personal fall arrest system, heat stress, and personal hygiene; understand the different levels of heat stress and the dangers they pose to workers; gven a variety of job site scenarios, demonstrate safe work practices around the following hazards: electrical, ladders, scaffolds, housekeeping, falls, confined spaces, and hazardous atmospheres; understand what fire hazards exist in a controlled area and how to prepare for the occurrence of an accidental fire; define the following acronym and terms: clean room, equipment room, HVAC, shower room, and waste load-out area; list and explain four reasons for preplanning asbestos abatement operations; list the 12 steps in preparing the work area; define the purpose of decontamination on an asbestos abatement project; list the elements of the decontamination chamber and explain the function of each; explain the purpose and function of a negative pressure air unit; using several example spaces, calculate the number of machines needed to meet air change requirements; given the proper materials and equipment, prepare the work area, set up the required number of negative air machines, and set up a three-chamber decontamination unit according to the guidelines in this chapter; define the following: amended water, encapsulation, enclosure, glove bag, HEPA vacuum, and NESHAP; describe the difference between bridging and penetrating sealants; list three advantages and seven disadvantages of encapsulation; list three advantages and seven disadvantages of enclosure; list 10 tools commonly used with a glove bag; describe the two stages of asbestos abatement; list the 19 steps of the final cleanup; define the following terms and acronyms: aggressive sampling, area sampling, breathing zone, bulk sampling, PCM, personal sampling, PLM, static sampling, and TEM; explain how and why air sampling is done on an asbestos abatement project; list the two analytical methods used in final clearance of asbestos abatement projects; explain the difference between static sampling and aggressive sampling; describe bulk sampling, settled dust sampling, and wipe sampling methods; list and briefly describe the limitations of three analytical methods used in asbestos abatement; and explain the purpose for taking area samples from outside the work area (but inside the building) and from outside the building.
Major topics include: work area preparation, decontamination facility construction and use, abatement techniques, and cleanup procedures. Special emphasis is placed on following proper procedures and developing safe work habits. The course meets all OSHA requirements and is mandatory for all workers involved in Class I and Class II asbestos abatement work. The course exceeds EPA’s 32-hour minimum course requirements, as stipulated under 40 CFR Part 763.
In the lower division baccalaureate /associate degree category, 2 semester hours in Industrial Technology (4/16) (4/21 revalidation).
80 hours.
April 2011 – Present.
Upon successful completion of the course, students will be able to: list and explain the three general hazard categories on a hazardous waste site, and how to recognize them; describe and give examples of the following four types of chemical hazards: toxic, corrosive, carcinogen, and reactive; illustrate the fire triangle and explain its elements; illustrate the pH scale and explain how corrosive strength is measured; illustrate the flammable/explosive range and explain the importance of lower explosive limit (LEL) and upper explosive limit (UEL); explain oxygen deficiency and describe the two ways it can be caused; list, explain, and give examples of the physical states in which chemicals are commonly found; describe the two types of radiation, explain their differences, and give examples of both; list and describe three biological hazards that can be found on hazardous waste sites; explain how safety meetings contribute to safety on a hazardous waste site; define engineering controls and give four examples of engineering controls that might be used on a hazardous waste site; list, explain, and give examples of the two main approaches used to reduce or prevent accidents, injuries, and illnesses on hazardous waste sites; list and explain the three routes of entry for chemicals into the body; explain the difference between a local health effect and a systemic health effect and give three examples of each; explain the difference between a prompt health effect and a delayed health effect and give three examples of each; list and explain the respiratory system’s three natural defenses; list the six physical warning signs of chemical exposure; demonstrate how to properly self-monitor for heat stress and evaluate the results; describe at least two conditions that indicate occupational noise has reached a hazardous level; describe at least two signs or symptoms of temporary hearing loss; given the PPE, demonstrate how to properly wear and/or insert hearing protection; list the steps for and be able to demonstrate the proper lifting procedure; explain “oxygen deficiency” and describe the two main causes for its occurrence; list four main body systems and explain how chemical and physical hazards may affect them; list and describe the signs and symptoms of the four stages of heat stress; explain the liver’s role in the body’s defense system; describe the following three air-purifying respirators and list the assigned protection factor APF for each: ½ Face APR, FFAPR, and PAPR; list and explain at least six limitations of APRs; list and explain the three filter series and three filter efficiency levels for particulate filters; explain the terms “breakthrough” and “warning properties” and list four steps that should be taken if breakthrough occurs; explain the term assigned protection factor (APF) for a respirator and, given five different respirators, state the correct APF of the five examples; explain the abbreviation “MUC” for a respirator and, given five different respirators, calculate the correct MUC in the five different respirators; explain the differences between an air-purifying respirator and an atmosphere supplying respirator; explain the differences between the three delivery systems for breathing air: continuous flow, demand, and pressure demand; explain how a supplied air respirator (SAR) works; list three limitations of the SAR and the APFs for both the SAR and the SAR with escape; explain how an SCBA works, its limitations, and APF; given the proper equipment, demonstrate the proper procedures for refilling an SCBA cylinder (hands-on); list and explain the nine requirements of a respiratory protection program; explain the difference between a qualitative and a quantitative fit test, and give two examples of each; demonstrate and explain the proper procedure for performing a positive and negative user seal check on an APR; given a variety of respirators, demonstrate donning, use, doffing, and maintenance of each respirator according to the guidelines of this course (hands-on); list and explain the three different types of leakage that can occur with chemical protective clothing; list and explain five factors that can affect your work-mission duration on an environmental project; describe the four “levels of protection” that may be used when doing hazardous waste work; given a variety of protective clothing and specific instructions for donning and doffing of various work ensembles, demonstrate the correct procedures according to the guidelines of this course (hands-on); explain the purpose of decontamination on hazardous waste sites and list three pathways of exposure; explain the terms “contamination avoidance” and “contamination transfer” and list three safe work procedures associated with each; describe the difference between physical removal and chemical removal as methods of decontamination; given three emergency scenarios, describe when decontamination should take place and a possible decontamination procedure for each scenario; given mock scenarios, perform decontamination appropriately, according to the guidelines of this chapter; list and explain the 10 topics of information that are required in a Site Safety and Health Plan (SSHP); describe five scenarios on a hazardous waste site where additional site-specific training is required; list and explain five different elements of a site control program; explain the purpose of the “buddy system” and describe three activities that “buddies” perform on a hazardous waste site; list and explain the two types of communication systems that must be used on hazardous waste sites; list four examples of waste-related emergencies and four examples of non-waste related emergencies; explain the importance of training and drills in an emergency response plan; explain the importance of standard operating procedures (SOP) and why they need to be followed on hazardous waste sites; given a mock unidentified hazardous materials container, list and identify the “clues” to look for when performing a preliminary visual inspection; describe different sampling techniques used to identify hazardous materials; describe the appropriate response and handling procedures for the following site-specific hazards: radioactive materials, explosive or shock-sensitive waste, bulging drums, laboratory packs, leaking, open, or deteriorated drums, and buried drums; given an empty overpack drum and a mock damaged drum, demonstrate three methods of manually overpacking the drum; define the term “characterization” and explain how and why it is done on a hazardous waste site; given the proper equipment, containers, and personal protective equipment (PPE), explain and demonstrate methods for collecting bulk samples on a mock hazardous waste site using the following devices: auger and thin-walled tube sampler and drum thief and COLIWASA; list and explain the three safe work practices that should be used when storing hazardous materials; given the proper materials, equipment, and several mock hazardous waste containers, construct and organize a contained staging area according to the guidelines in this course; explain and compare the differences, advantages, and disadvantages of direct-reading instruments (DRIs) versus laboratory analysis of workplace samples; describe five situations on a hazardous waste site where workplace monitoring would usually be required; given the proper equipment, conduct the required workspace monitoring for a mock (practice) permit-required confined space entry; using various sample chemicals and the proper equipment, demonstrate how to use and interpret the readings of colorimetric detector tubes and a photoionization detector (PID); list and explain the appropriate responses if a personal monitoring device or sampling pump fails; define a confined space, giving three characteristics; list two categories of confined spaces and give examples of each; list two factors that lead to fatal injuries in confined spaces; describe the four characteristics of a permit-required confined space; locate the titles of the 17 paragraphs of the OSHA Hazardous Waste Operations and Emergency Response Standard and describe the contents of each paragraph; explain the employee responsibilities contained in the Occupational Safety and Health Act (OSH Act); describe the 11 rights an employee has under Section 11(c) of the OSH Act; describe three conditions found in 29 CFR 1977.12 that must be present for OSHA’s “right to refuse hazardous work” to apply; describe the purpose of the following environmental laws: RCRA, CERCLA, SARA, Clean Air Act, NESHAPS, Clean Water Act, and Hazardous Material Transportation Act; explain CERCLA and what the Superfund Act did for the nation; explain SARA and the changes it made; list and explain the nine steps of the Superfund process and the corresponding guidelines for community relations at each step; explain the worker’s role in the community relations process; list and explain the guidelines that should be followed when answering questions or discussing hazardous waste site operations; explain the meaning of the term “groundwater” and describe its importance; list and explain the four phases of the hydrologic cycle; explain the meaning of and the differences between “point sources” and “nonpoint sources” of contamination; given the proper equipment and working with a partner, prepare a flip chart diagram of a selected remediation technology and deliver a 5-minute classroom presentation about this technology.
Major topics covered in the course are the safe and productive ways of working on hazardous waste remediation sites. Special emphasis is placed on following procedures and developing safe work habits.
In the associate/certificate degree category, 3 semester hours in Construction Technology (4/16) (4/21 revalidation).
40 hours.
April 2011 – Present.
Upon successful completion of the course, students will be able to: list and explain the three general hazard categories on a hazardous waste site, and how to recognize them; describe and give examples of these four types of chemical hazards: toxic, corrosive, carcinogen, and reactive; illustrate the fire triangle and tetrahedron and explain their elements; illustrate the pH scale and explain how corrosive strength is measured; illustrate the flammable/explosive range and explain the importance of lower explosive limit (LEL) and upper explosive limit (UEL); explain oxygen deficiency and describe the two ways it can be caused; list, explain, and give examples of the physical states in which chemicals are commonly found; identify the two types of radiation, explain their differences, and give examples of both; list and describe three biological hazards that can be found on hazardous waste sites; explain how safety meetings contribute to safety on a hazardous waste site; define engineering controls and give four examples of engineering controls that might be used on a hazardous waste site; list, explain, and give examples of the two main approaches used to reduce or prevent accidents, injuries, and illnesses on hazardous waste sites; list and explain the three routes of entry for chemicals into the body; explain the difference between a local health effect and a systemic health effect and give an example of each; explain the difference between a prompt health effect and a delayed health effect and give three examples of each; list the six physical warning signs of chemical exposure; list and describe the signs and symptoms of the four stages of heat stress; explain the liver’s role in the body’s defense system; describe the following three air-purifying respirators and list the assigned protection factor APF for each: ½ Face APR, FFAPR, and PAPR; list and explain at least six limitations of APRs; list and explain the three filter series and three filter efficiency levels for particulate filters; explain the terms “breakthrough” and “warning properties” and list four steps that should be taken if breakthrough occurs; explain the term assigned protection factor (APF) for a respirator; explain the abbreviation “MUC” for a respirator and, given five different respirators, calculate the correct MUC in the five different respirators; explain the differences between an air-purifying respirator and an atmosphere supplying respirator; explain the differences between continuous flow, demand, and pressure demand; explain how a SAR works; list three limitations of the SAR and the APFs for both the SAR and the SAR with escape; explain how an SCBA works, its limitations, and APF; list and explain the nine requirements of a respiratory protection program; explain the difference between a qualitative and a quantitative fit test; demonstrate and explain the proper procedure for performing a user seal check on an APR; list and explain the three different types of leakage that can occur with chemical protective clothing; describe the four “levels of protection” that may be used when doing hazardous waste work; given a variety of protective clothing and specific instructions for donning and doffing of various work ensembles, demonstrate the correct procedures according to the guidelines of this course; explain the purpose of decontamination on hazardous waste sites and list three pathways of exposure; explain the terms contamination avoidance and contamination transfer and list three safe work procedures associated with each; describe the difference between physical removal and chemical removal as methods of decontamination; given three emergency scenarios, describe when decontamination should take place and a possible decontamination procedure for each scenario; given mock scenarios, perform decontamination appropriately, according to the guidelines of this course; list and explain the 10 topics of information that are required in a Site Safety and Health Plan (SSHP); describe five scenarios on a hazardous waste site where additional site-specific training is required; list and explain five different elements of a site control program; explain the purpose of the “buddy system” and describe three activities that “buddies” perform on a hazardous waste site; list and explain the two types of communication systems that must be used on hazardous waste sites; list four examples of waste-related emergencies and four examples of non-waste related emergencies; explain the importance of training and drills in an emergency response plan; explain the importance of standard operating procedures (SOP) and why they need to be followed on hazardous waste sites; list and identify the “clues” to look for when performing a preliminary visual inspection of containers; list two sampling techniques used to identify hazardous materials; describe the appropriate response and handling procedures for the following site-specific hazards: radioactive materials, explosive or shock-sensitive waste, bulging drums, laboratory packs, leaking, open, or deteriorated drums, and buried drums; define the term “characterization” and explain how and why it is done; list and explain the three safe work practices that should be used when storing hazardous materials; explain and compare the differences, advantages, and disadvantages of direct-reading instruments (DRIs) vs. laboratory analysis of workplace samples; describe five situations on a hazardous waste site where workplace monitoring would usually be required; using various sample chemicals, demonstrate how to use and interpret the readings of a colorimetric tube and a multigas meter; list and explain the appropriate responses if a personal monitoring device or sampling pump fails; define a confined space, giving three characteristics; list two categories of confined spaces and give examples of each; list two factors that lead to fatal injuries in confined spaces; describe the four characteristics of a permit-required confined space; locate the titles of the 17 paragraphs of the OSHA Hazardous Waste Operations and Emergency Response Standard (HAZWOPER, 29CFR 1910.120) and describe the contents of each paragraph; explain the employee responsibilities contained in the Occupational Safety and Health Act (OSH Act); describe the 11 rights an employee has under Section 11(c) of the OSH Act; describe three conditions found in 29 CFR 1977.12 that must be present for OSHA’s “right to refuse hazardous work” to apply; explain CERCLA and what the Superfund Act did for the nation; explain SARA and the changes that it made; explain the worker’s role in the community relations process; list and explain the guidelines that should be followed when answering questions or discussing hazardous waste site operations.
Major topics include safe and productive ways of working on hazardous waste remediation sites. Special emphasis is placed on following procedures and developing safe work habits.
In the lower division baccalaureate /associate degree category, 2 semester hours in Construction Technology (4/16) (4/21 revalidation).
24 hours.
April 2011 – Present.
Upon successful completion of the course, students will be able to: list and explain the three general hazard categories on a hazardous waste site, and how to recognize them; describe and give examples of the following four types of chemical hazards: toxic, corrosive, carcinogen, and reactive; illustrate the fire triangle and explain its elements; illustrate the pH scale and explain how corrosive strength is measured; illustrate the flammable/explosive range and explain the importance of lower explosive limit (LEL) and upper explosive limit (UEL); explain oxygen deficiency and describe the two ways it can be caused; list, explain, and give examples of the physical states in which chemicals are commonly found; describe the two types of radiation, explain their differences, and give examples of both; list and describe three biological hazards that can be found on hazardous waste sites; explain how Safety Meetings contribute to safety on a hazardous waste site; define engineering controls and give four examples of engineering controls that might be used on a hazardous waste site; list, explain, and give examples of the two main approaches used to reduce or prevent accidents, injuries, and illnesses on hazardous waste sites; list and explain the three routes of entry for chemicals into the body; explain the difference between a local health effect and a systemic health, and give three examples of each; explain the difference between a prompt health effect and a delayed health effect, and give three examples of each; list and explain the respiratory system’s three natural defenses; list the six physical warning signs of chemical exposure; explain oxygen deficiency and describe the two main causes for its occurrences; list the steps of the proper lifting procedure; list and describe the signs and symptoms of the four stages of heat stress; explain the purpose of decontamination on hazardous waste sites and list three pathways of exposure; explain the terms “contamination avoidance” and “contamination transfer” and list three safe work procedures associated with each; describe the difference between physical removal and chemical removal as methods of decontamination; list and explain the 10 topics of information that are required in a Site Safety and Health Plan (SSHP); describe five scenarios on a hazardous waste site where additional site-specific training is required; list and explain five different elements of a site control program; explain the purpose of the “buddy system” and describe three activities that “buddies” perform on a hazardous waste site; list and explain the two types of communication systems that must be used on hazardous waste sites; list four examples of waste-related emergencies and four examples of non-waste-related emergencies; explain the importance of training and drills in an emergency response plan; explain the importance of standard operating procedures (SOPs) and why they need to be followed on hazardous waste sites; list two sampling techniques used to identify hazardous materials; describe the appropriate response and handling procedures for the following site-specific hazards: radioactive materials, explosive or shock-sensitive waste, bulging drums, laboratory packs, leaking, open, or deteriorated drums, and buried drums; define the term “characterization” and explain how and why it is done on a hazardous waste site; list and explain the three safe work practices that should be used when storing hazardous materials; explain and compare the differences, advantages, and disadvantages of direct-reading instruments (DRIs) versus laboratory analysis of workplace samples; describe five situations on a hazardous waste site where workplace monitoring would usually be required; using various sample chemicals, demonstrate how to use and interpret the readings of a colorimetric tube and a multigas meter; explain the importance of daily calibration checks; list and explain the appropriate responses if a personal monitoring device or sampling pump fails; define a confined space, giving three characteristics; list two categories of confined spaces and give examples of each; list two factors that lead to fatal injuries in confined spaces; describe the four characteristics of a permit-required confined space; locate the titles of the 17 paragraphs of the OSHA Hazardous Waste Operations and Emergency Response Standard (HAZWOPER, 29CFR 1910.120) and describe the contents of each paragraph; explain the employee responsibilities contained in the Occupational Safety and Health Act (OSH Act); describe the 11 rights an employee has under Section 11(c) of the OSH Act; describe three conditions found in 29 CFR 1977.12 that must be present for OSHA’s ‘right to refuse hazardous work’ to apply; explain CERCLA and what the Superfund Act did for the nation; explain SARA and the changes it made; explain the worker’s role in the community relations process; and explain the guidelines that should be followed when answering questions from the public or media, regarding site cleanup operations.
Major topics include: pevious training and work experiences that provide practical application of previously learned concepts to real life situations. Additionally, the course covers new technologies, regulatory updates, recent advances, and lessons learned.
In the associate/certificate degree category, 1 semester hour in Construction Technology (4/16) (4/21 revalidation).
16 hours.
April 2011 – Present.
Upon successful completion of the course, students will be able to: define leadership; list six skills or characteristics of an effective leader; list the six basic steps of decision making; list and explain the five key points of effective communication; explain how body language influences verbal communication; list the points to consider when evaluating a message; explain how attitude can impact communication; list the steps to follow when evaluating written communication; list the steps to follow when planning a safety meeting; explain the supervisor’s responsibilities as they relate to the site-specific safety and health plan; explain the term “living document”; identify the 14 sections of a typical site-specific safety and health plan; state the objective of a Quality Assurance Project Plan; list the typical information recorded on a chain-of-custody form; name three other kinds of records the supervisor might be responsible for maintaining; list the three categories of stress; list the four phases of disaster response; list six signs of cognitive stress response; list six signs of physical stress response; list six signs of emotional stress response; explain the purpose of debriefing sessions; list and explain the 11 requirements OSHA has established for a minimal acceptable respirator program (MARP); perform a quantitative fit test according to OSHA guidelines; perform a qualitative respirator fit test according to OSHA guidelines; list the criteria that must be factored when selecting PPE for site workers; identify and explain the two ground rules of decontamination; state at least four reasons why workplace monitoring is performed; explain the supervisor’s role in the workplace monitoring program; explain the difference between an instrument calibration and a bump check; give information that the supervisor or worker on a cleanup site can give to the media; list the times when the media may become involved with a site; state the employer’s “general duty” under the OSH Act; explain why workers’ legal rights should be respected on a hazardous waste project, even more so than on a general construction project; explain the workers’ basic rights and protections under the “Whistleblower” program; explain management’s role as it relates to safety on the job site; explain the worker’s role as it relates to safety on the job site; identify how the supervisor fits into the “big picture” of workers’ legal rights; and state the possible legal consequences of deliberate or willful disregard of safety standards on the part of the supervisor, if such action results in a serious injury or death.
Major topics include leadership skills, prepare for emergencies and understand the legal rights and requirements of hazardous waste workers. This course builds upon the information provided in the 80-hour Hazardous Waste Worker course.
In the associate/certificate degree category, 1 semester hour in Construction Technology (4/16) (4/21 revalidation).
40 hours.
April 2011 – Present.
Upon successful completion of the course, students will be able to: identify the two major forms of lead used as pigments in paint; explain three ways lead poisoning can occur in residential housing; identify three examples of recreational exposure to lead; list four occupations that greatly increase lead exposure; identify the melting and boiling points of lead; list the main responsibilities of a lead-abatement supervisor; identify the routes of entry for lead entering the body; explain where lead goes and where it is stored once in the body; list the acute and chronic effects associated with lead exposure; list the body systems that can be damaged by lead exposure; explain the special hazards that lead poses for children; list the two types of medical tests used for detecting lead; explain how chelating agents help rid the body of lead; define Title X, and list four conditions Title X defines as lead-based paint hazards; define Toxic Substance Control Act (TSCA) and list the three goals of TSCA section 402 concerning training and certification of lead abatement workers; list the action level and permissible exposure limit (PEL) for lead under the OSHA Interim Lead Standard for Construction (29 CFR 1926.62); list the three exposure task categories, provide examples for each task and list the corresponding exposure range; describe the compliance methods the employer must follow to ensure worker exposures are reduced to or below the PEL; list three practices that are prohibited by OSHA in a lead-regulated area; explain the importance of medical surveillance to a lead abatement worker; explain medical removal protection, and describe how it works; describe the 3 types of air-purifying respirators (APRs) and list the assigned protection factor of each; list and explain at least six limitations of APRs; explain the term HEPA and state the efficiency level of a HEPA filter; explain the term “assigned protection factor” (APF) for a respirator and, given three different respirators, state the correct APF for each; explain the acronym MUC as it relates to a respirator and calculate the correct MUC for three sample respirators; explain the difference between an air purifying respirator and an atmosphere supplying respirator; explain the difference between a qualitative and quantitative fit test and give an example of each; demonstrate and explain the proper procedure for performing a positive and negative user seal check on an APR; list the personal protective equipment (PPE) used by lead abatement workers; define the following terms and acronyms: accident, confined space, GFCI, hazardous atmospheres, LFL, UFL, oxygen deficiency, lock out and tag out, personal fall arrest system, heat stress and personal hygiene; list the different levels of heat stress and describe the dangers they pose to workers; given a variety of job scenarios, describe safe work practices around the following hazards: electrical, ladders, scaffolds, housekeeping, falls, confined spaces, hazardous atmospheres; describe the fire hazards that exist in a controlled area and how to prepare for the occurrence of an accidental fire; list and identify the materials and equipment needed to perform wipe sampling; describe and demonstrate the procedure for wipe sampling lead-contaminated dust; list and identify the materials and equipment needed to sample paint chips; describe and demonstrate the paint chip sampling procedures; list and identify the materials and equipment needed to perform soil sampling; describe and demonstrate soil-sampling procedures; define clearance sampling and describe the procedures involved in performing clearance sampling; list the U.S. Department of Housing and Urban Development (HUD) clearance levels for lead found in dust (using wipe sampling) for floors, interior windowsills, and window troughs; list the three parties that should maintain records for all abatement, interim control, risk assessment, inspection, and clearance results, and explain why; explain the responsibilities of the inspector on a lead abatement project; identify the most common inspection method used to determine the presence of lead-based paint; list the procedures defined in the inspection report to determine the presence of lead-based paint; identify the surfaces in a residence that may require abatement if they are in violation of EPA 40 CFR 745; explain the purpose of a risk assessment when trying to determine the presence of lead-based paint; list the responsibilities of a certified risk assessor; explain the role the risk assessor has in educating various parties involved in lead poisoning prevention; describe how to use at least four abatement methods; demonstrate proficiency in at least two abatement methods; demonstrate how to perform final cleanup on a lead abatement job; explain the importance of clearance inspections; list the soil and exterior abatement procedures; describe the procedures for preparing the occupant protection plan; explain the two specific situations in which the use of a negative pressure zone would be appropriate in a residential setting; given a variety of scenarios of lead abatement projects, list step-by-step procedures to ensure resident protection; list three types of insurance that owners, consultants, and contractors should have for lead abatement projects; describe the basis on which a commercial general liability (CGL) policy should be written; explain how the CGL policy should be specifically endorsed or written; describe each of the following types of insurance policies and explain their purpose: occurrence-based, errors and omissions, claims-made, liability; list and define the three types of bonds; list the three types of liability; and define tort liability.
Major topics focus on expansion of the Lead Abatement Worker course and supervisory training so students can lead abatement projects. This course is mandatory for all workers responsible for supervising lead-based paint activities in target housing and child-occupied facilities and exceeds the EPA’s minimum training requirements of 32 hours of training.
In the lower division baccalaureate/associate degree category, 2 semester hours in Construction Technology or Construction Safety (4/16) (4/21 revalidation). NOTE: Course content is duplicative of the Lead Abatement Worker LEAD.W course. Care should be taken to avoid awarding duplicate credit.
40 hours.
April 2011 – Present.
Upon successful completion of the course, students will be able to: identify the two major forms of lead used as pigments in paint; explain three ways lead poisoning can occur in residential housing; identify three examples of recreational exposure to lead; list four occupations that greatly increase lead exposure; identify the routes of entry for lead entering the body; explain where lead goes and where it is stored once in the body; list the acute and chronic effects associated with lead exposure; list the body systems that can be damaged by lead exposure; explain the special hazards that lead poses for children; list the two types of medical tests used for detecting lead; explain how chelating agents help rid the body of lead; define Title X, and list four conditions Title X defines as lead-based paint hazards; define Toxic Substance Control Act (TSCA) and list the three goals of TSCA section 402 concerning training and certification of lead abatement workers; list the action level and permissible exposure limit (PEL) for lead under the OSHA Interim Lead Standard for Construction (29 CFR 1926.62); list the three exposure task categories, provide examples for each task and list the corresponding exposure range; describe the compliance methods the employer must follow to ensure worker exposures are reduced to or below the PEL; list three practices that are prohibited by OSHA in a lead-regulated area; explain the importance of medical surveillance to a lead abatement worker; describe the three types of air-purifying respirators (APRs) and list the assigned protection factor of each; list and explain at least six limitations of APRs; explain the term HEPA and state the efficiency level of a HEPA filter; explain the term “assigned protection factor” (APF) for a respirator and, given three different respirators, state the correct APF for each; explain the acronym MUC as it relates to a respirator and calculate the correct MUC for three sample respirators; explain the difference between an air purifying respirator and an atmosphere supplying respirator; explain the difference between a qualitative and quantitative fit test and give an example of each; demonstrate and explain the proper procedure for performing a positive and negative user seal check on an APR; list the personal protective equipment (PPE) used by lead abatement workers; define the following terms and acronyms: accident, confined space, GFCI, hazardous atmospheres, LFL, UFL, oxygen deficiency, lock out and tag out, personal fall arrest system, heat stress and personal hygiene; list the different levels of heat stress and describe the dangers they pose to workers; given a variety of job scenarios, describe safe work practices around the following hazards: electrical, ladders, scaffolds, housekeeping, falls, confined spaces, hazardous atmospheres; describe the fire hazards that exist in a controlled area and how to prepare for the occurrence of an accidental fire; list the four sampling methods used to identify the presence of lead; explain how the X-ray fluorescence (XRF) instrument determines the presence of lead; explain how the personal air sampling method is used to identify the presence of lead; list two ways dust samples can be collected; explain the responsibilities of the inspector on a lead abatement project; identify the most common inspection method used to determine the presence of lead-based paint; list the procedures defined in the inspection report to determine the presence of lead-based paint; identify the surfaces in a residence that may require abatement if they are in violation of EPA 40 CFR 745; explain the purpose of a risk assessment when trying to determine the presence of lead-based paint; list the responsibilities of a certified risk assessor; explain the role the risk assessor has in educating various parties involved in lead poisoning prevention; describe how to use at least four abatement methods; demonstrate proficiency in at least two abatement methods; demonstrate how to perform final cleanup on a lead abatement job; explain the importance of clearance inspections; list the soil and exterior abatement procedures; list the 10 legal rights workers have under the Occupational Safety and Health Act of 1970; list seven responsibilities workers have under the Occupational Safety and Health Act of 1970; list seven steps workers should follow if they are punished for exercising any right under the OSH Act; identify three control methods used to eliminate lead exposure; identify the four methods used to remove lead paint from steel structures; demonstrate the chemical removal method for lead paint on steel structures; demonstrate the manual removal method for removing lead paint from steel structures.
Major topics covered in the course are designed to prepare students to work safely and productively on lead abatement projects. The course meets all Occupational Safety and Health Administration (OSHA) and Environmental Protection Agency (EPA) training requirements under 29 CFR Part 1926.1101 and 40 CFR Part 745.225, respectively. The course is mandatory for all workers conducting lead-based paint activities in target housing and child-occupied facilities. The Lead Abatement Worker course far exceeds EPA’s minimum training requirements of 16 hours of training (with 8 hours of laboratory) for workers by fully covering required topics and dedicating a total of 40 hours to instruction, of which 8 hours are hands-on activities.
In the lower division baccalaureate /associate degree category, 2 semester hours in Construction Technology or Construction Safety (4/16) (4/21 revalidation). NOTE: Course content is duplicative of the Lead Abatement Supervisor LEAD.S course. Care should be taken to avoid awarding duplicate credit.
24 hours.
April 2011 – Present.
Upon successful completion of the course, students will be able to: define the following terms: sick building syndrome, spores, and microbial contamination; list six causes of indoor air pollution; identify and describe the ideal environment for mold growth; identify at least two common symptoms associated with mold exposure; define the following terms: aspergillus, bacteria, fungi, HP, mycotoxins, ODTS, penicillium, stachybotrys chartarum (Atra), trichothecene mycotoxin, and viruses; identify the routes of entry for fungi to enter the body; list at least three reasons for performing work area monitoring and sampling; list at least three methods of sampling used to detect and identify the presence of microbial contamination; describe the following three air purifying respirators and list the assigned protection factor (APF) for each: Half-face Air Purifying Respirator, Full-face Air Purifying Respirator, and Full-face Powered Air Purifying Respirator; list and explain at least six limitations of Air Purifying Respirators (APRs); list and explain the three filter series and three filter efficiency levels for particulate filters; explain the terms “breakthrough” and “warning properties” and list four steps that should be taken if breakthrough occurs; explain the term “assigned protection factor” (APF) and how it relates to a respirator; correctly state the APF for the three respirators mentioned above; explain the abbreviation MUC and give the MUC for each of the same respirators mentioned above; list and explain the nine requirements of a Respiratory Protection Program; explain the difference between a qualitative and quantitative fit test, and give an example of each; identify and describe at least three elements of work area preparation that should be completed before any microbial remediation can begin; list at least two of the most common chemicals used to destroy microbial organisms; describe the proper mixture for a bleach/water solution used during microbial remediation; given the proper materials, mix a bleach/water solution in the correct proportion according to the guidelines of this course (hands-on); given a space, calculate its volume and determine the appropriate number of negative air units to achieve four air exchanges per hour; given a space, tools, and equipment, contain the space and set up a negative pressure enclosure according to the procedures recommended in this course (hands-on); given the tools, materials, equipment and PPE and a mock work area, demonstrate remediation of microbial contamination according to the guidelines of this course (hands-on); explain the importance of decontamination during microbial remediation projects and list four ways that workers may be exposed; define decontamination; list the elements of a three-chamber decontamination unit and explain the function of each; working in small groups, construct a three-chamber decontamination unit according to the guidelines in this course; given a full-face APR, a protective suit, boots, and gloves, simulate the decontamination process according to the guidelines in this course.
Major topics focus on workers who will be employed on microbial remediation projects or job sites having the potential of having mold, moisture, and mildew hazards. The course is designed for those with no previous Asbestos or Lead Abatement Worker training. Additional hours are dedicated to hands-on activities.
In the lower division baccalaureate/associate degree category, 2 semester hours in Environmental Health and Safety, and Environmental Science (4/16) (4/21 revalidation).
24 hours.
April 2011 – Present.
Upon successful completion of the course, students will be able to: state the purpose and types of emergency alarms and identify the correct response to each; identify the NRC Form 3; explain the worker’s Rights and Responsibilities; identify the different structures that make up the nuclear power plant; identify the components that make up a nuclear reactor; differentiate from among the following terms: fission, chain reaction, critical, sub-critical, and supercritical; explain the difference between a pressurized and boiling water reactor; identify the parts that make up the atom; list the four (4) types of ionizing radiation list the three main types of ionizing radiation and give the unique characteristics, such as composition, penetration, shielding, hazard concern and properties for each type; differentiate between ionizing and non-ionizing radiation; identify the following terms: ionizing radiation, half-life, radioactive decay, radioactive material, and radiation; identify the quality factor for each type of radiation; define Rad, Rem, and QF; identify the following exposure terms: Rem, Mrem, dose rate, roentgen, Curie, Rad; list the three (3) main categories of natural sources of radiation exposure; distinguish between Natural and Artificial radiation; state the occupational radiation exposure limits for the following: whole body, extremities, skin, pregnant sorker, total organ dose; identify the radiosensitivity of various body organs; match the following items to the best definition: somatic effect, radiosensitivity, DNA, genetic effect, Acute Radiation Syndrome, and the Law of Bergonie and Tribondeau; distinguish between acute and chronic effects; identify the potential biological effect of different acute whole body radiation doses; calculate a worker’s dose using the following equation: DOSE = Dose Rate x Time; match the following terms to the best answer: dose, time, half value layer, distance, and shielding; calculate the dose rate at a given distance using the following equation: d1/(d2)2 = d3, where d1 = Dose rate at the source, d2 = Distance from the source, and d3 = Dose rate at new distance; define the term ALARA; list the basic types of radiation detection instruments, give their purpose, and the limitations of each personal dosimeter device; obtain readings during a field survey using the Ludlum Model 3 survey meter; list the basic types of personal dosimeters, give their purpose, and the limitations of each personal dosimeter device; read and calibrate the Victoreen Model 541R Pocket Dosimeter and charge it using the Victoreen Model 2000A dosimeter charge; match the following terms with the appropriate definition or example: loose contamination, fixed contamination, total contamination, airborne contamination, waterborne contamination, internal contamination, external contamination, radioactive contamination; describe the purpose of a Frisker; demonstrate the procedures for personal frisking; list the reasons for decontamination; describe the process of setting up a decontamination procedure; demonstrate the procedures for personal decontamination; identify the following terms: personnel contamination monitor, counts per minute, disintegrations per minute, swipe, and smear; describe the difference between Air Monitoring and Air Sampling; demonstrate the procedures for donning and doffing Anti-C clothing; list the requirements and benefits of a Quality Assurance Program; summarize the requirements of a Quality Assurance Program; list the worker’s obligation as related to security; define contraband and give three (3) examples of it; define what is meant by a drug-free workplace and describe the workers’ responsibilities; describe what is meant by fitness for duty; identify contractor responsibilities; identify common hazards associated with construction activities; and identify hazard protections.
Major topics are designed for workers involved in the maintenance and shutdown activities at nuclear power plants or whose job assignment involves unescorted access entry into areas controlled for radiological purposes, clean-up of radiological contaminated waste sites or whose job assignment involves unescorted entry into areas controlled for radiological purposes.
In the lower division baccalaureate/associate degree category, 1 semester hour in Radiological Science or Fundamentals of Health Physics (4/16) (4/21 revalidation).
24 hours.
April 2011 – Present.
Upon successful completion of the course, students will be able to: describe at least three characteristics of a confined space; identify two factors that lead to fatal injuries in confined spaces; describe the four characteristics of a permit-required confined space; define and describe the three types of atmospheric hazards found in confined spaces; list the five types of airborne hazards; list and describe the six types of physical hazards found in confined spaces; list the four types of health effects from toxic chemicals; list three routes of entry for chemicals to enter the body; define and describe warning signs of acute and chronic exposure to toxic chemicals; list and describe the four types of heat stress; describe ways to prevent heat stress; explain and compare the differences, advantages, and disadvantages of direct-reading instruments (DRIs) versus laboratory analysis of workplace samples; identify two situations where atmospheric monitoring would typically be required during confined space entry operations; given the proper equipment, conduct the required workplace monitoring for permit-required confined space entry; given various sample chemicals and the proper equipment, demonstrate the use and interpret the readings of colorimetric detector tubes and a multi-gas meter; list and explain the appropriate responses if a personal monitoring device or sampling pump fails; list the components of a permit-required confined space entry program; explain the purposes of an entry permit; list at least five of the 15 required elements of an entry permit; list the required elements of pre-entry atmospheric testing; identify the members of a confined space entry team and describe the duties of each; describe at least two instances when training is required for confined space entry; define ventilation; list and describe at least three problems associated with ventilating a confined space; list at least four controllable atmospheric hazards and the methods to control them; explain supply and exhaust ventilation; explain the advantages and disadvantages of each; list at least five planning considerations to be given when ventilating confined spaces and explain why each is important; given a mock confined space, ventilation blower and manufacturers purge chart, calculate the amount of time to ventilate the confined space; evaluate a mock confined space for atmospheric hazards; plan and set up ventilation to remove hazards from the space in the time specified on a purge chart; define the following terms: affected employee, authorized employee, energy isolating device, energy source, lockout, lockout device, tagout, tagout device; identify the four categories of hazardous energy and the means for controlling each; define the roles of affected and authorized employees when working under an energy control program; given a scenario, identify potential sources of hazardous energy and a method for controlling each; explain the terms “assigned protection factor” (APF) and “maximum use concentration”; explain the differences between an air-purifying respirator (APR) and an atmosphere-supplying respirator; describe three types of APRs and give the APF for each; list and explain at least six limitations of APRs; list and explain the three filter series and three filter-efficiency levels for particulate filters; explain the terms “breakthrough” and “warning properties” and list four steps that should be taken if breakthrough occurs; explain the differences among three breathing air delivery systems for breathing air: continuous flow, demand, and pressure demand; explain how a supplied airline respirator (SAR) works; list three limitations of the SAR and the APFs for both the SAR and the SAR with escape; explain how a self-contained breathing apparatus (SCBA) works, its limitations, and APF; explain the difference between a qualitative and a quantitative fit test, and give two examples of each; demonstrate the proper procedures for inspecting and donning a full-face APR; explain and demonstrate the proper procedure for performing a positive and negative user seal check on an APR; demonstrate the proper procedure for inspecting and donning an SCBA.
Major topics include: hazard recognition, atmospheric monitoring, entry plans policy and procedures, personal protective equipment (PPE), and hazard mitigation. The course is designed to provide students with the knowledge and skills associated with working in and around confined spaces.
In the lower division baccalaureate /associate degree category, 1 semester hour in Construction Safety (4/16) (4/21 revalidation).
32 hours.
April 2011 – Present.
Upon successful completion of the course, students will be able to: identify the three basic particles of an atom and the charge and location of each; define ionization; define ionizing radiation, radioactive material, and radioactive contamination; distinguish between ionizing radiation and non-ionizing radiation; define radioactivity and radioactive half-life; state the four basic types of ionizing radiation; identify the following for each of the four types of ionizing radiation: physical characteristics, range/shielding, biological hazard(s), and sources; identify the units used to measure radiation, contamination, and radioactivity; convert rem to millirem and millirem to rem; identify the major sources of natural background and man-made radiation; identify the sources of and average annual dose to the general population from natural background and man-made radiation; state the method by which radiation causes damage to cells; identify the possible effects of radiation on cells; define the terms “acute dose” and “chronic dose”; state examples of a chronic radiation dose; define the terms “somatic effect” and “heritable effect”; state the potential effects associated with prenatal radiation doses; compare the biological risks from chronic radiation doses to health risks workers are subjected to in industry and daily life; state the purposes of the facility administrative control levels; identify the U.S. Dept. of Energy (DOE) radiation dose limits, DOE administrative control level, and facility administrative control levels; state the site policy concerning prenatal radiation exposure; identify the employee’s responsibility concerning radiation dose limits and administrative control levels; describe the action a worker should take if he/she suspects that dose limits or administrative control levels are being approached or exceeded; state the ALARA concept; state the DOE/site management policy for the ALARA program; identify the responsibilities of management, Radiological Control Organization, and the radiological worker regarding the ALARA program; identify the basic protective measures of time, distance, and shielding; identify methods for reducing external and internal radiation dose; state the pathways radioactive material can enter the body; identify methods a radiological worker can use to minimize radioactive waste; state the purpose of each of the personnel dosimeter devices used at the site; identify worker responsibilities concerning each of the external personnel dosimeter devices used at the site; state the purpose of each type of internal monitoring method used; identify worker responsibilities concerning internal monitoring programs; state the methods for obtaining radiation dose records; identify worker responsibilities for reporting radiation doses received from other sites and from medical applications; define fixed, removable and airborne contamination; state the sources of radioactive contamination; state the appropriate response to a spill of radioactive material; identify methods used to control radioactive contamination; identify the proper use of protective clothing; identify the purpose and use of personnel contamination monitors; identify the normal methods used for decontamination; define contamination, high contamination, and airborne radioactivity areas; identify the requirements for entering, working in, and exiting contamination, high contamination, and airborne radioactivity areas; state the purpose of and information found on radiological work permits (RWPs); identify the worker’s responsibilities in using Radiological Work Permits; identify the colors and symbols used on radiological postings; state the radiological and disciplinary consequences of disregarding radiological postings, signs, and labels; define the areas controlled for radiological purposes; identify the minimum requirements for entering, working in, and exiting: radiological buffer areas, radiation areas, radioactive material areas, soil contamination areas, fixed contamination areas; state the personnel frisking requirements when exiting Radiological Buffer Areas; state the purpose and types of emergency alarms; identify the correct responses to emergencies and/or alarms; state the possible consequences of disregarding radiological alarms; and state the DOE and site administrative occupational emergency radiation dose guidelines.
Major topics include: radiation, the health effects caused by radiation exposure, DOE radiation dose limits and control measures, the “As Low as Reasonably Achievable (ALARA)” concept, protective measures to avoid and/or reduce radiation exposure, proper work techniques, use of dosimetry, proper monitoring techniques, decontamination techniques, and proper entry and exit from controlled areas. This course prepares students to work on sites with radioactive elements overseen by the U.S. Department of Energy (DOE). Special emphasis is placed on following proper procedures and developing safe work habits.
In the lower division baccalaureate/associate degree category, 1 semester hour in Radiological Sciences or Fundamentals of Health Physics (4/16) (4/21 revalidation).
16 hours.
April 2011 – Present.
Upon successful completion of the course, students will be able to: develop a brief general outline of the overall restoration process for employees including: initial or pre-inspection, inspection, monitoring and documentation, restoring structure and contents, coordination, completion; interpret and explain written organizational policies and procedures to help employees perform their jobs according to employer rules and expectations; identify company health and safety programs to ensure compliance with regulations and employee protection (OSHA and EPA); identify hazards unique to the restoration project and identify appropriate actions required to address them; comply with federal, state, and local safety and regulatory requirements; organize work teams and schedule employee work assignments; ensure the scope of work is followed and standardized procedures and practices are met; employ planning and time management skills and tools to monitor, plan, and control day-to-day activities required to enhance results and complete work tasks in a restoration project; use quality-control processes to minimize errors, maximize operational effectiveness, and expedite workflow; update work plans and schedules; use organizational and project management skills to improve workflow, minimize costs, and monitor and evaluate project; define insurance industry terms including: Actual Cash Value (ACV), Replacement Cost Value (RCV), depreciation, and “hold back”; interpret standard insurance policies including the identification of coverages and exclusions; identify three types of insurance adjusters; review sample claim files effectively; describe the basic Insurance Process/Relationship Chain of Events; explain the difference between open and closed drying systems; demonstrate how to use industry-required psychrometric equipment in a mock work area; demonstrate recording psychrometric readings; organize psychrometric reading documentation; calculate three items and record them on a psychrometric chart: dry bulb temperature, relative humidity (RH), specific humidity (humidity ratio); dxplain basic property damage protocols; pretest for restorability (fire/smoke damage, water damage) in a mock work area; create the proper loss inspection and mitigation documentation to determine the scope of the loss and any pre-existing issues in a mock work area; describe the proper documentation of required forms to justify procedures and project timeline; describe the appropriate project inspections and/or testing with required agencies and/or legal parties; describe an inventory control system; conduct contents inventory in a mock work area; describe how to order and schedule labor, equipment and materials; explain liability with equipment; ensure safe and efficient use, installation, and setup of all project equipment; describe personal and job site safety rules and regulations that maintain safe and healthful working conditions and environments; describe how to maintain property and equipment necessary for project activities; describe how to oversee maintenance schedules for vehicles, materials and equipment; and explain how to use appropriate technology and computer-based equipment (containing embedded computers or processors) to control devices and for business applications.
Major topics are designed to build upon information provided in the Restoration Technician course. Students learn about managing staff and projects, understanding insurance practices, understanding psychrometric readings, and calculating materials and equipment. Special emphasis is placed on following proper procedures and developing safe work habits.
In the lower division baccalaureate/associate degree category, 1 semester hour in Construction Management (4/16) (4/21 revalidation).
40 hours.
April 2011 – Present.
Upon successful completion of the course, students will be able to: identify a systematic method for cataloging materials that will be removed and returned to the work site; identify appropriate cleaning methods for food service, upholstered, and porcelain surfaces; explain the importance of a complete inventory listing destroyed, damaged and pre-existing damages; describe basic principles for proper restoration; list criteria for evaluating whether damaged furnishings and fixtures are restorable; explain cleaning processes used for content restoration: dry, wet, spray and wipe, foam, abrasive, immersion; identify what types of materials are effectively cleaned with each process; explain how moisture content from direct contact and absorption of water from the air is critical to drying; define the term psychrometry; explain how a psychrometric chart is read; identify types of equipment used to scope the area affected by water; determine the type of action required to prevent further structural damage: containment barriers, tarp, and shrink wrap; identify potential contaminants in a damaged structure; explain safety regulations for removing contaminants from a structure; explain the removal of water through dehumidification; list types of dehumidification equipment: refrigerant and desiccant; explain the process of controlling microorganisms; explain the role of demolition in the restoration industry; explain the process or deodorization as it applies to disinfecting a damaged structure; operate equipment used to restore water and smoke damaged structures: inspection and monitoring tools and extraction tools; list and explain sanitizing agents used to arrest growth of bacteria, fungi, mildew, and other microorganisms; identify equipment used to neutralize odors; explain health hazards associated with biological and chemical contaminants; define pathogenic substances; identify three pathogenic substances that may require removal and disposal from a contaminated environment (blood, bodily fluids, and tissue); list personal protective equipment required when removing biological and chemical contaminants; explain complex damages caused by fire and smoke; identify four types of soot: wet smoke residues, dry smoke residues, protein residue, and fuel oil soot; identify other possible contaminants: tear gas, finger print powder, and fire extinguisher residue; explain the cleaning process used for each type of soot; describe the three methods of soot/smoke and other contaminant removal: HEPA vacuuming, dry sponging, and chemical washing; explain options for cleaning carpet, based on the type of carpet; identify four specialized carpet-cleaning methods: bonnet cleaning, steam cleaning/hot water extraction, pre-conditioning and rinse, and dry cleaning; describe deodorization methods used for carpet cleaning; explain cleaning methods appropriate for blinds and drapery; identify fabric manufacturers’ recommendations for each material to be cleaned; identify cleaning methods for blinds and drapery based on the type of fabric from which they are made; explain when demolition of wall and ceilings is the correct option; identify the cleaning method to apply according to the extent of damage to ceilings and walls; discuss the principles necessary to deodorize odors according to type of damage to ceilings and walls; identify appropriate actions to prevent further damage to electronics and machinery; list three types of cleaning processes for electronics and machinery: HEPA vacuuming, chemical washing, and contamination free drying; explain techniques for reassembling electronics and machinery; describe the importance of ventilation in the cleanup process; identify procedures to follow when cleaning the air duct system; identify components of the HVAC system that must be cleaned: evaporators and cooling coils, fans and blower wheels; perform air duct cleaning according to industry standards for cleaning HVAC heating and cooling system; describe how to maintain HVAC heating and cooling system following Category 1 damage; explain methods of deodorization; list three fundamental principles for deodorizing an affected area: remove source, clean surfaces, and seal surfaces; and describe equipment used to deodorize an affected area.
Major topics are geared toward commercial cleanup activities associated with fire and/or flood damaged structures. The Restoration Technician course is designed for students who have received previous training in hazardous waste remediation, asbestos, and lead abatement as this course centers on the theory, application, and practices associated with restoration projects.
In the associate/certificate degree category, 2 semester hours in Construction Methods or Construction Technology (4/16) (4/21 revalidation).
Safety and Health
12 hours.
April 2011 – Present.
Upon successful completion of the course, students will be able to: define the following terms: benching, competent person, cross braces, excavation, hazardous atmosphere, sheeting, shield, slope ratio, sloping, trench, uprights and wales; describe three warning signs of a possible trench cave-in; describe two types of protective systems for excavations; describe the soil characteristics of type A, B, and C soil, and state the sloping requirements for each soil type; list the OSHA requirements for access and egress from excavations, given a set of construction scenarios, determine the access/egress requirements for each scenario (to within an accuracy of at least 80%); given the proper tools and equipment and working in teams, demonstrate the installation of timber tight shoring, shoring with screw jack bracing, and hydraulic shoring, according to the guidelines in this course.
Major topics are designed for workers who work in trenches and excavations. Students learn about OSHA’s standards for building protective systems in trenches and excavations, and other regulations to ensure safety on a job site. Students also learn how to install different kinds of protective systems, with special emphasis placed on following proper techniques and developing safe work habits.
In the associate/certificate degree category, 1 semester hour in Construction Technology (4/16) (4/21 revalidation).
Utilities
24 hours.
April 2011 – Present.
Upon successful completion of the course, students will be able to: describe each of the three green roof classification types: extensive, intensive and semi-intensive; list the benefits of green roofs; demonstrate how to convert from English to metric system of measurement; identify and use metric nuts, bolts and tools; demonstrate the safe and proper use of a heat gun; adhere to all roof safety precautions; adhere to OSHA’s fall protection regulations; demonstrate how to interpret green roof plans and specifications and identify potential issues within the plan; demonstrate how to install green roof components; describe the different types of soil media and how to obtain proper depth and grading; describe the types of roof pavers and paver installation methods; demonstrate how to level roof pavers to installation caliber; identify elements of green roof irrigation systems and describe installation/repair methods; identify plant types commonly used for green roofs; and describe proper plant handling, planting techniques and plant maintenance.
Major topics center around various types of green roofs, the safety hazards associated with the installation of green roofs, and the practices and procedures used during installation of the roof.
In the associate/certificate degree category, 1 semester hour in Construction Technology (4/16) (4/21 revalidation).
40 hours.
April 2011 – Present.
Upon successful completion of the course, students will be able to: define the following terms: bench mark, horizontal, level, offset, percent of grade, plumb, rate per foot, station, and vertical; describe the use of common construction referencing methods to locate object as manholes or utilities; given reference points for an object, locate the object within .25’; describe how stationing systems are used to locate measurements within the project; given a series of hub grades, use squaring principles to set offset stakes at 25’ intervals to establish a trench line; given a grade sheet with a set of elevations, calculate elevations and elevation changes using a rate per foot or percentage of slope; given a partially completed cut sheet, calculate the cut or fill for each station; given an established trench line, set up and demonstrate the use of a pipe laser to check for proper grade within the excavation; demonstrate the set up of the pipe laser in a manhole to check for line and grade; demonstrate the correct set up of a transit level; given a set of elevation hubs and working on a team, calculate each elevation to within +/- .02’; define the following terms: benching, shield, competent person, slope ratio, cross braces, sloping, excavation, trench, hazardous atmosphere, uprights, sheeting, and wales; describe three warning signs of a possible trench cave-in; describe two types of protective systems for excavations; describe the soil characteristics of type A, B, and C soil, and state the sloping requirements for each soil type; list the OSHA requirements for access to and egress from excavations; given a set of construction scenarios, determine the access/egress requirements for each scenario; given the proper tools and equipment, and working in teams, demonstrate the installation of timber tight shoring, shoring with screw jack bracing, and hydraulic shoring; define the following terms: building sewer, gravity flow, main, sanitary sewer, sanitary sewer system, sewage, sewers or sewer systems, lateral, and manhole; identify and describe the purpose of the tools and equipment used in sanitary sewer installation; working as part of a team, demonstrate the installation of 110 feet of PVC pipe, and demonstrate installation of PVC laterals; list and describe the tools and equipment used in storm sewer installation; working as part of a team, demonstrate the installation of storm sewer pipe; identify and describe the purpose of the tools and equipment used for repair and tie-in of PVC and concrete pipe; working as part of a team, demonstrate the repair of PVC and concrete pipe; describe and demonstrate the set-up and operation of low-pressure air testing equipment on sewer lines; identify and describe the purpose of the tools and equipment used form manhole invert construction; working as part of a team, demonstrate the construction and shaping of an invert within a manhole; describe five types of pipe used for storm drain and sub drain systems; identify and explain the purpose of each of the following tools and pipe appurtenances: all-thread rod, tee bolt, dresser coupling, wrap-around repair clamp; describe and demonstrate joining pipe sections using mechanical and Tyton (push-on) joint connections; describe and demonstrate Ductile Iron water pipe installation and assembly techniques; given a drawing of a fire hydrant assembly, assemble the hydrant within tolerance and according to the drawing; describe and demonstrate hydrostatic testing procedures for Ductile Iron pipe and demonstrate test pump set-up and operation; given a formula and problems related to leakage during hydrostatic testing, calculate the maximum allowable leakage for each problem; describe and identify the following tools and appurtenances: corporation stop, curb stop, tapping saddle, tapping machine, flaring tool; identify the components of a Mueller model B-100 tapping machine, inspect each component, and set up the machine; describe and demonstrate the procedures for direct tapping and assembling of a water service connection; describe and demonstrate the maintenance procedures for the Mueller model B-100 tapping machine; describe the protocol for using a central “One Call” number; given a list of “One Call” numbers and a state or county, locate the correct number; given the need to excavate near a utility, describe notification requirements and location services provided by the local utility company; and describe and demonstrate the purpose and process of probing and potholing a utility.
Major topics provide the basic knowledge and skills that CCLs need to work safely in trenches, and correctly install, tap, and repair PVC, Ductile Iron and concrete pipe.
In the lower division baccalaureate/associate degree category, 1 semester hour in Pipeline Technology or Construction Technology (4/16) (4/21 revalidation).
64 hours.
April 2011 – Present.
Upon successful completion of the course, students will be able to: define the term “The Spread”; name the chain of command on a pipeline job; list seven employee obligations; name three general hazards associated with working on a pipeline; explain the “common sense” approach to hazard recognition; define what a “pinch point” is; list five pieces of personal protective equipment (PPE) commonly used on pipeline projects; give the minimum clearance between overhead power lines and any part of a crane or load; explain the use of “goal posts”; name two causes of trench failures or cave-ins; list the three main protective systems used to protect against cave-ins; identify the weakest soil type, and describe how it affects the slope of the trench walls; explain the difference between shoring and shielding; specify at what height a walkway over a trench bottom requires handrails; identify one of the hazards of confined spaces; name the type of information found on safety data sheets (SDSs); explain why there must be a controlled access area set up when the device used to x-ray welds is in use; explain why hooking and unhooking mud mats is dangerous; name at least four actions you can take to prevent heat stress; name at least four actions you can take to prevent cold stress; demonstrate proper lifting technique; name the most commonly injured part of the back, and explain why it is so frequently injured; list at least five types of work that Construction Craft Laborers (CCLs) perform on a pipeline project; describe the process of rigging pipe joints using a side boom with wire rope slings and hooks; explain the benefits of using a vacuum lift; demonstrate three methods for securing loads; explain the difference between right of way (ROW) stakes and ditch stakes; describe the purpose of station numbers; name two reasons for having overnight fire watches; list the steps for opening and closing a fence gap; list the duties of a CCL when using pumps to dewater a trench; describe two ways of making yourself more visible to an equipment operator when giving signals; explain when voice commands need to be used; state what skids are used for; name a safety precaution you should take when flagging traffic; describe the correct method for crossing equipment over paved roads; list three types of protective barriers installed by the environmental crew; define “soil compaction”; give an example of a problem caused by backfill soil that wasn’t compacted properly; list three of the factors to consider when determining the amount of compaction needed to compact backfill to the proper density; name two types of compaction equipment that a CCL will routinely operate; explain how and when to clean the tracks of equipment; list three “good housekeeping” tasks; explain the two main purposes of a warehouse; describe one task that Construction Craft Laborers (CCLs) perform during the setup of a jobsite warehouse; list and describe three ongoing tasks that CCLs do at a warehouse; describe the process of setting up a storage trailer; describe how to safely unload pipe being delivered to a job; state what a “staging area” is and what it is used for; describe the proper steps involved in preparing drinking water for a crew; explain what a berm is and what it is used for; explain why “good housekeeping” and organization are important; list three hazards of warehouse work; explain the main task of the Line Locating Crew; paraphrase the main sequence of steps the Line Locating Crew goes through to locate an underground line; list three hazards of rupturing an underground utility line; name three steps that are taken before excavation begins; explain what “One-Call” systems are and what purpose they serve; identify five indicators from records or from the field that may signal the presence of an underground utility; tell what an alignment sheet is and what information it provides; correctly identify at least five of the nine color-coded surface markings; list two common types of temporary markers; explain what an M-scope is and what it is used for; explain what potholing is; demonstrate the process of potholing an underground utility line; tell what a protective barrier is; list at least three signs you may see during potholing that may indicate an underground line is nearby; explain what a hydro-vac is and what it is used for; tell why it is important to inspect the coating of uncovered lines; list the information that should be listed on temporary markings that are installed after a “find”; list at least four things CCLs do during the line locating process; describe the main task of the fence crew; identify one thing you need to do before clearing brush; describe a situation where existing fence is saved for reuse; describe a gap; demonstrate the ability to build a temporary gap, including the use of a power auger and construction of an H-brace; explain the general sequence used to build a straight gap; explain the general sequence used to build an angled gap; describe a power augur and what it is used for; explain how to properly open and close a gap; explain why it is important to close a gap securely; identify the PPE commonly worn by members of the fence crew; describe the general work of the clearing crew; list three tasks performed by CCLs on the clearing crew; tell why it is important that all work remain within the limits of the right-of-way; describe what a point of intersection (PI) is and where it is used; list four observable signs to help recognize the ROW; describe the most common type of marking device; list five colors of flagging, and explain what they stand for; explain two of the considerations the must be taken into account during controlled burning operations; explain why operating chippers can be dangerous, and list six safety procedures to help minimize this risk; list three things a swamper does while assisting heavy equipment operators on the clearing crew; describe the type of work done by the environmental crew; list three reasons why environmental protection is important; list three types of erosion control methods; explain the purpose of a silt fence and demonstrate how to correctly set up and dismantle a silt fence; list two types of ditch breaks and where they are used; identify three common hazards of environmental protection work; describe the general work of the grade crew; explain why grading the ROW is important; list two specific tasks of the grad crew; list at least one role of a CCL on a grade crew; describe the role of a swamper; list three important precautions that the grade crew should observe; explain the main job of the ditch crew; describe what a soft plug and hard plug are; list one task that must be completed when excavating a ditch in a wet area; list two types of heavy equipment commonly used to excavate a ditch; list three duties of CCLs on ditch crews; explain what offset stakes are and what they are used for; list two do’s and don’ts when guiding an equipment operator; explain why it is important to open and close gaps properly; identify the risk experienced by the ditch crew that results in the most injuries and fatalities each year; list two methods of preventing cave-ins; state at what ditch depth cave-in prevention measures become required; describe the main task of the rock ditch crew; describe two tasks of the drill crew; describe two tasks of the powder crew; describe the main task of the matting crew; list two common types of heavy equipment used when matting; list three hazards associated with working on the rock ditch crew; list the main method used to clear an area and announce an upcoming blast; list three tasks of the rock ditch crew that require additional training; explain the main task of a skid crew; tell what a skid is and what it is used for; explain why it is important to keep pipe up off the ground; explain why proper spacing of skids on the ROW is important; identify four common configurations of skids: stacked, slide, crib/pigpen, and crotch; demonstrate the ability to build safe and secure support structures out of skids; explain the reason for adding padding to skids, and list common padding materials; list five activities done during the mainline activities phase of pipeline construction; state the methods for protecting and securing pipe for hauling; identify two of the common materials used to pad skids; explain when and why you need to double up pipe joints when stringing them along the ROW; name two markings written on the pipe by the bending engineer and his or her helpers; describe the process of rigging the pipe and putting it through the bending machine; identify two common types of bends; give the reason for rolling seams when setting up pipe in preparation for welding; explain what carry-back is and what you should do if you lose it; state the reason why special PPE is required when working in the vicinity of the end-facing machine; describe the hazard associated with weld X-ray equipment used to inspect welds on a pipeline project; define nightcaps; explain why the coating on the pipeline is important; explain why proper sandblasting is important to the coating process; give a definition for “sand pot”; demonstrate the process of setting up sandblasting equipment; demonstrate how to use a sand blaster to prepare pipe for coating; name three of the basic maintenance duties you will perform on sandblasting equipment; describe the proper PPE for sandblasting with silica sand; list the three types of epoxy coatings and demonstrate how to apply them; demonstrate how to apply a shrink sleeve; explain the two types of tape, and demonstrate the methods for applying them; give a brief explanation of what a Safety Data Sheet (SDS) is; demonstrate how to jeep the pipe (use a holiday detector); describe and demonstrate three patching methods for repairing holidays; identify four hazards of working on the coating crew; define dewatering; demonstrate how to set up a 3” gas-powered water pump; describe, in general, what a CCL will be doing to maintain water pumps; describe ditch soil conditions that may adversely affect pipe coating; state the minimum depth of soil that is required for bedding material; explain how to rig a pipe for lowering-in using a roller cradle; describe how to rig a pipe for lowering-in using a lowering-in sling; describe the need and requirements for protecting the pipe and coating during placement (lowering-in); explain how skids are used in the trench during lowering-in; describe how to prevent damage to coating during backfill operations; explain why there is a CCL assigned to perform fire watch duties during the tie-in process; define a pup joint; explain what a bell hole is; give a brief explanation of why zinc ribbon is placed in the ditch along both sides of the pipeline; describe how to verify pipeline wall thickness and location; demonstrate how CAD-weld test leads onto a pipe; describe how to select a location for an exothermic weld (CAD-weld), the exothermic weld size, and the appropriate furnace/mold; describe the final steps associated with test lead installation, as part of the cathodic protection system; describe the difference between a cradle auger boring machine and a track auger boring machine; explain what a “deadman” is and how it is used when boring with a cradle auger boring machine; explain what slurry is and how it is used when boring or drilling; describe the process, when using horizontal directional drilling, of obtaining the appropriately sized hole for the pipe being used; list three hazards associated with boring under roads; explain why you could have problems from stopping while pulling the pipe through the hole passing under a river, made by a horizontal directional drilling machine; explain how the cutting head of a horizontal directional drilling machine is “steered”; list three of the cleanup duties CCLs will be expected to perform; explain the main purpose of testing a pipeline before it is put into service; name the most common method of testing a pipe; identify and describe the purpose of the “pig” that is used for pipeline testing; describe the general steps to hydro-test a section of pipeline; explain what a caliper pig is and what it is used for; tell why pressure test results have to be certified; explain why it is important to take accurate temperature readings during pressure testing; describe the biggest hazard that results from pressure testing on a pipeline; describe the general work scope of the cleanup and restoration crew; explain the differences between clean up in urban areas compared to rural areas; describe what must be done to roads and driveways that were disturbed during construction; list three things that are removed by the cleanup and restoration crew; explain three types of permanent erosion control devices; tell where fences need to get rebuilt; list four locations where permanent pipeline markers need to be installed; identify three of the five pieces of information that must appear on a pipeline mile marker; list three of the four things that need to be verified when inspecting an existing pipeline marker; explain the things on private property that must be restored to their original, pre-construction, condition; list three hazards encountered while doing cleanup and restoration work; describe what type of work is considered “specialty work”; list two of the three methods of crossing a river; describe what dredging is and where it is used; describe the general process of floating a pipe across a waterway; describe what happens at a “push site”; explain what an aerial crossing is; describe three tasks that are done at a fabrication yard; explain what “special fabricated devices” are and what purpose they serve on the pipeline; list three things Construction Craft Laborers (CCLs) do at a fabrication yard; define “double jointing,” and tell why it is done; explain why some sections of pipe have concrete installed on them; explain what happens at “pipe yard”; explain what a “tie-down anchor” is and what it is used for; list three hazards of specialty work; describe what is done at a central pipeline control center using a supervisory control and data acquisition (SCADA) control system; explain what a sphere is and what it is used for; describe how the safety record of pipelines compares to other transportation methods; explain what an emergency management plan is and why it is important; describe how pipelines are cleaned of build-up on the inside walls of the pipe; describe what an “aerial” pipeline inspection is and what purpose it serves; describe what a “smart pig” is and what it is used for; explain when the coating on a pipe must be inspected; list three defects that may be found when inspecting the coating of an exposed pipe; list five things that may be found when inspecting the structural integrity of an exposed pipe; list two reasons why an excavation area around an existing pipe may have to be extended; describe a “clock spring repair” and how its use affects the structural integrity of the pipe; and list four abnormal operation conditions that warrant notifying a designated operating representative.
Major topics include: employee obligations, chain of command on a pipeline, general hazards and precautions, trench and excavation safety, soil testing and identification, potholing and underground utility lines, the duties of the various crews (fence, ditch, clearing, etc.), cleaning and inspecting pipes, and fabrication yards. Several of the topics require students to perform tasks or demonstrate skills being taught. Special emphasis is placed on following proper techniques, developing safe work habits, and recognizing unsafe work conditions.
In the lower division baccalaureate/associate degree category, 2 semester hours in Pipeline Technology or Construction Technology (4/16) (4/21 revalidation).
16 hours.
April 2011 – Present.
Upon successful completion of the course, students will be able to: describe at a high level what a thermal system and photovoltaic system does and list the key components of each; list the key components to each type of system; explain how each system either heats the water or generates electricity; convert from an English to metric measurement system; use all materials according to manufacturer’s instructions; properly stage a roof, adhering to OSHA guidelines; prepare a commercial site; use safety steps for ground installations; identify whether a solar site is a viable site; recognize roof characteristics, and how each impacts the solar panel installation; describe and mitigate ground installation issues; install solar panels on a residential structure; install solar panels on a commercial structure; and install solar panels on the ground or on a structure they have built to support the panels.
Major topics introduce students to safe installation techniques for a variety of solar panel installations, including ground mounted and roof mounted. Roof mounted installation covers various roof types, including pitched, flat, asphalt, and rubber. Special emphasis is placed on following proper procedures and developing safe work habits.
In the associate/certificate degree category, 1 semester hour in Construction Technology (4/16) (4/21 revalidation).